Mold costs depe…
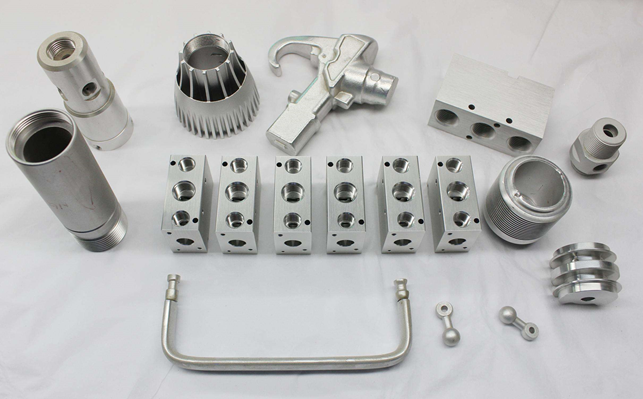
Hand board surface treatment process ⑩: Anodic Oxidation
Taking metal or alloy parts as anodes, oxide films are formed on their surfaces by electrolysis. Metal oxide film changes the surface state and properties, such as surface coloring, improving corrosion resistance, enhancing wear resistance and hardness, protecting metal surface and so on. The thin layer of oxide film has a large number of micropores, which can absorb various lubricants and is suitable for manufacturing engine cylinders or other wear-resistant parts; The membrane has strong microporous adsorption capacity and can be colored into various beautiful and gorgeous colors. Non ferrous metals or their alloys (such as magnesium, aluminum and their alloys) can be anodized. This method is widely used in mechanical parts, aircraft and automobile parts, precision instruments and radio equipment, daily necessities and architectural decoration.
Anodic oxidation treatment:
1. Protective property
2. Decorative
3. Insulation
4. Improve the adhesion with organic coatings
5. Improve the adhesion with organic covering layer, etc
Difference between anodic oxidation and conductive oxidation:
1. Anodic oxidation is carried out under the condition of high voltage. It is an electrochemical reaction process; Conductive oxidation (also known as chemical oxidation) does not need electricity, but only needs to be soaked in liquid medicine. It is a pure chemical reaction.
2. Anodic oxidation takes a long time, often tens of minutes, while conductive oxidation takes only a few tens of seconds.
3. The film produced by anodic oxidation has several microns to tens of microns, and is hard and wear-resistant, while the film produced by conductive oxidation is only 0.01-0.15 microns. Wear resistance is not very good, but it can conduct electricity and resist atmospheric corrosion, which is its advantage.
4. The oxide film is not conductive, but because the film generated by conductive oxidation is very thin, it is conductive.