Mold costs depe…
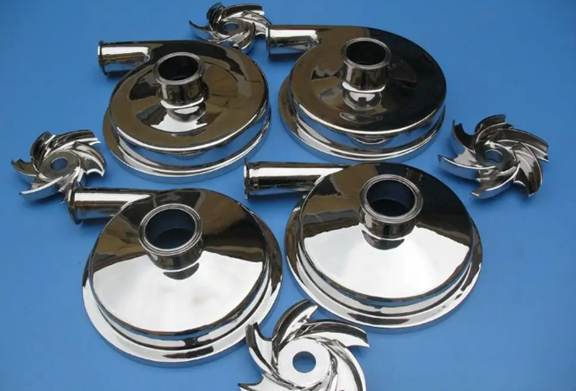
Hand board surface treatment process ⑤: Polishing
Polishing refers to the processing method of reducing the surface roughness of the workpiece by mechanical, chemical or electrochemical action, so as to obtain a bright and flat surface. Hand polishing can not improve the dimensional accuracy or geometric accuracy of the workpiece, but for the purpose of obtaining smooth surface or mirror gloss, and sometimes used to eliminate gloss (extinction).
There are many kinds of hand polishing materials, which are generally divided into: polishing wax, polishing cloth wheel, nylon wheel, hemp wheel, thread wheel, wind wheel, miscellaneous cloth wheel, etc.
Different workpiece polishing has different polishing processes, and different processes need to use different polishing consumables. The traditional hand polishing process is divided into three processes: rough polishing, semi fine polishing and fine polishing. Today, with the rapid development of polishing technology, the hand polishing process has also been developed and improved rapidly. The polishing process is shortened to two processes, and even some workpieces can be polished in one process.
Taking the polishing of hand plate aluminum alloy crafts as an example, there are two common methods of polishing aluminum alloy. They are: acid polishing and alkaline polishing. Hand polishing is nothing more than to get a smooth and flat surface of the workpiece. It is a method of hand surface treatment. Different polishing methods have their own advantages and disadvantages.
Take the chemical polishing and electrochemical polishing of aluminum alloy alkaline polishing as an example:
1. Alkaline chemical polishing:
Advantages of aluminum mirror polishing and aluminum alloy polishing: it is applicable to all kinds of aluminum and aluminum alloys. It can also obtain satisfactory results for cast aluminum and die-casting aluminum (with low impurity content and sand blasting treatment) (aluminum base color and luster). No nitric acid, no Huanglong pollution.
Disadvantages: the amount of aluminum dissolved is large and the luster is general. It is not suitable for precision parts and parts with mirror luster requirements
2. Electrochemical polishing
Advantages: no hexavalent chromium pollution, low cost, mirror luster can be obtained.
Disadvantages: the process is complex, requiring rectifier power supply, fixture and anode moving device.
To sum up, different polishing methods have their advantages and disadvantages. Therefore, in the process of aluminum alloy polishing, reasonable methods should be selected according to the specific workpiece conditions, so as to achieve the best polishing effect.