Mold costs depe…
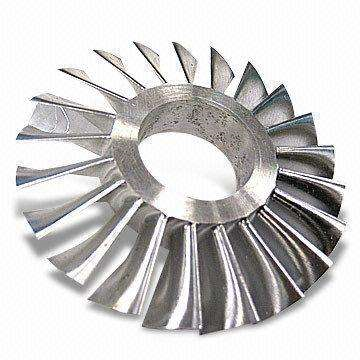
Five axis NC milling solution for integral impeller blade
Integral impeller is the core component of turbo engine and turbocharged engine. It is widely used in energy and power, aerospace, petrochemical industry, metallurgy and other industries. It is a representative, standardized and typical channel complex part. The machining means, machining accuracy and machining surface quality of its profile directly affect the aerodynamic performance and mechanical efficiency of the engine, and have a decisive impact on the performance of the engine. Integral impeller has become a typical difficult to machine part because of its complex surface and high machining precision.
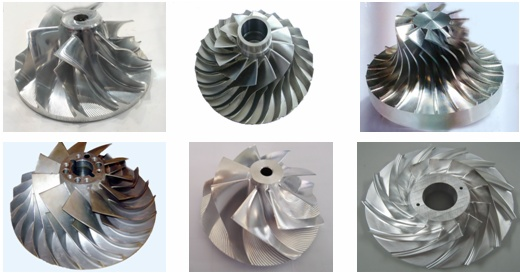
With the increasing market demand for turbine engine, it is more and more necessary to realize the efficient machining of integral impeller. At present, the common materials of integral impeller are aluminum alloy, titanium alloy, stainless steel, etc.
The complexity of impeller processing mainly lies in the complexity of blade surface modeling. Its surface can be divided into ruled surface and non ruled surface according to the forming principle, and the ruled surface can be divided into developable ruled surface and non developable ruled surface. Five axis NC milling has the advantages of good flexibility, high machining efficiency and wide application. It is one of the common methods for integral impeller machining. According to the different surface shape of impeller, two kinds of methods are usually used in machining on NC machine tools, namely point milling method and side milling method.
Due to the complex shape of the integral impeller and the large distortion of the blade, the machining is very easy to interfere. Therefore, the difficulty of machining is the rough and finish machining of the runner and blade. In the NC machining process of integral impeller, taper ball end milling cutter is often used in order to minimize over cutting and interference caused by cutter, and the cutter can still have good rigidity when machining narrow channel.
In order to make the impeller meet the requirements of aerodynamics, the blade often adopts the structure of large torsion angle and variable fillet at the root, which puts forward higher requirements for the processing of the impeller. The machining technical requirements of integral impeller include geometric requirements such as size, shape, position and surface roughness, as well as mechanical, physical and chemical properties. The impeller blade must have good surface quality. The accuracy is generally concentrated on the blade surface, hub surface and blade root surface, and the surface roughness value shall be less than Ra0 8um。
In order to meet the above requirements, the following problems are often encountered in the processing of integral impeller:
① The overall impeller has narrow flow passage, relatively long blades and low stiffness. It belongs to thin-walled parts and is very easy to deform during processing. In the process of machining, due to the action of its own structure and external cutting force, the inlet of the runner and the upper end of the blade will produce vibration marks. Sometimes, in order to avoid shock marks, it is often necessary to change the sharpness of the tool, which will produce burrs at the inlet, outlet and blade edge of the runner. In order to ensure the surface quality of the integral impeller, the cutting tool needs to have enough chip removal space and appropriate sharpness under the condition of sufficient rigidity.
② The blade depth at the narrowest part of the flow channel is far more than the tool diameter, and the space of adjacent blades is very small. During corner clearing, the tool diameter is small, and the tool is easy to break. The control of cutting depth is also the key technology of machining.
③ The surface of the integral impeller is a free-form surface, with narrow flow channel, serious blade distortion and obvious backward tilt trend. It is very easy to interfere during processing, which makes it difficult to process. Because some impellers have auxiliary blades, in order to avoid interference, the curved surface should be machined in sections. Therefore, it is difficult to ensure the consistency of the machined surface.
④ Considering that the integral impeller rotates at a high speed in the actual work, with a speed of 30000-50000 revolutions, it is necessary to prevent vibration and reduce noise, so the requirements for dynamic balance are high, which improves the requirements for machine tools and cutting tools. It is necessary to save the processing beat and ensure the stability and symmetry of cutting.
Considering the rigidity of machine tool, cutter, fixture and integral impeller, designing reasonable cutter structure and selecting appropriate manufacturing process can meet the manufacturing requirements of integral impeller.
[express statement] this article is reprinted from the Internet. The purpose of reprinting is to convey more information. It does not mean that this website agrees with its views and is responsible for its authenticity. The copyright of this article belongs to the original author. The content is the author’s personal point of view. Skynet only provides reference and does not constitute any investment and application suggestions. If you need to reprint, please contact the original source. Skynet is committed to providing you with content information with attitude, temperature and height.