Mold costs depe…
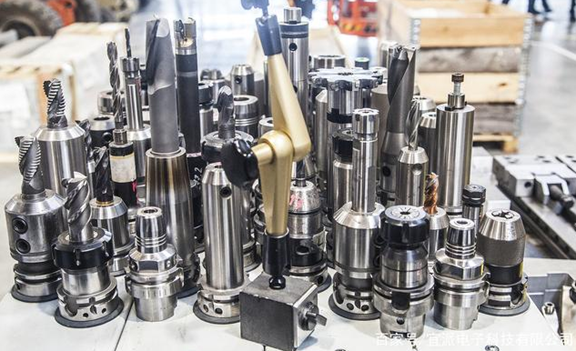
Common cutting tools for CNC machining (III): Geometric parameters
The basic requirement for the cutting tool to be able to cut metal is that the cutting tool must be harder than the material to be cut, and the material to be cut must have enough force to be fixed, so that the tool can cut into the workpiece when applying force. After these requirements are met, the second is to have enough power to overcome the resistance of workpiece materials. In addition, the geometry of the tool will also affect the actual cutting effect and even the result. Choosing proper tool geometry can increase tool life, maintain machining accuracy, reduce cutting power… And so on. The common tool related geometry is as follows: 1. Tool edge angle; 2. Chip removal tank; 3. Over center and non over center tools; 4. Number of blades;
1. Tool edge angle
1.1 cutting edge angle — rake angle
The bevel angle can be changed from positive value to negative value, as shown in the figure below. In terms of cutting force and required power, the tool tip angle formed by the positive and oblique angle is small, the tool can easily cut into the workpiece, and the chip outflow and removal is smooth, which can reduce the cutting pressure, so the cutting efficiency is large. However, too large positive and oblique angle forms a sharp knife point, so the knife edge is fragile and easy to wear or crack. On the contrary, the negative bevel angle has a strong cutting edge and high edge strength, which is suitable for cutting high-strength materials.
1.2. Tool edge angle — relief angle
Also known as the clearance angle, they are all positive. Its function is to avoid friction or interference of physical phenomena between the tool belly and the workpiece surface when the tool cuts into the workpiece, as shown in the figure below. The small clearance angle gives the cutting edge greater support. It is generally used for workpiece materials with high-strength mechanical properties. Large clearance angle can make the blade sharp, but the strength of the blade is reduced, which is easy to wear or crack. It is suitable for soft or low strength workpiece materials.
1.3 cutting edge angle – helix angle
The groove of this milling cutter is spiral, which can be divided into left spiral and right spiral, as follows. When the cutting edge enters the workpiece during cutting, as shown in the figure below, the cutting force F will instantly increase to the maximum. When the cutting edge leaves the workpiece, the cutting force decreases rapidly, which is the reason for the vibration during cutting. The function of helix angle at this time can prevent the cutting force from being too concentrated in one direction and disperse the cutting force in the other two directions – horizontal component FH and vertical component FV. When helix angle γ When it is larger, the horizontal component FH will become larger, resulting in tool swing during cutting; Helix angle γ The smaller the, the larger the vertical component FV will become. When the force holding the tool is not enough during cutting, the tool will be separated from the tool handle, which is very dangerous when rotating at high speed. The common helix angle is 30 ˚、 thirty-eight ˚、 forty-five ˚、 sixty ˚。
2. Chip chute
For the discharge of chips in cutting, the ideal chip treatment condition is that the chips will not interfere with or scratch the surface of the workpiece or impact the tool and hurt the workers when they flow out, so the chips should be able to break naturally into small fragments and be discharged to other places. Therefore, the chip control should not only consider the flow direction of the chip, but also make the chip break automatically. In order to meet this requirement, a design is generally made on the top surface of the cutter. The mechanism that can automatically limit the chip length is called chip breaker or chip breaker. The purpose is to make the chips curl rapidly and force the chips to break by the curling stress. The general chip removal groove design is shown in the lower right:
Groove width W: curl is formed when chips are generated. If the groove width is too large, the curl radius is large, and the curl stress is not enough to break chips; If it is too small, on the contrary, if the stress is too large, it is easy to crack the cutting edge.
Groove depth h: it affects the stability of chip outflow. If it is too deep, the curling force required when the chip flows to the groove shoulder is large, which is easy to cause the blade to break; If it is too shallow, the chips may leave without flowing to the groove shoulder, making the flow direction of chips difficult to control.
Groove shoulder R: refers to the part where the chip is rolled up by the chip breaking groove. It is related to whether the chip is rolled up smoothly or not, which directly affects the curling force. If the radius is too large, the chip is easy to slide up, and the curling stress may not be enough to break the chip; If the radius is too small, the chips are easy to be blocked and slide up, which will produce great extrusion stress.
3. Over center and non over center tools
When making the discarding round nose knife, usually the tool diameter D will be much larger than the R angle of the blade, so the blade will appear in the middle of the bottom without passing the center, that is, this area has no cutting ability, as shown in the figure below on the left. When the workpiece in the shape of machining hole or groove is encountered, the machining problem in the lower right figure will occur.
Although the size of the tool can enter these areas, because the blade has not passed the center, the blade will not cut the middle material and leave the Yellow columnar residual material in the figure. With the deeper processing, the height of the residual material will increase, and finally hit the bottom of the tool, causing tool damage. The over center tool is that its blade passes through the center, so there is no such problem, so it is also called drilling tool.
4. Number of blades;
The relationship between the number of cutting edges of the milling cutter and the cutting effect will be affected by the workpiece material, the shape of the milling cutter and the brightness of the machining surface. The milling cutter with more edges can obtain a smoother machining surface because of the cutting effect of more cutting edges. However, because there is no sufficient chip space to accommodate chips, it is easy to be disturbed by chips, and the strength of the blade will be weak.
Therefore, in general rough cutting, high feed, especially soft materials, there needs to be a large chip space, and the best way to provide chip space is to reduce the number of edges and increase the blade, which can not only increase the chip space, but also increase the strength of the blade, but also increase the regrinding times and service life of the milling cutter. Therefore, when considering the machining method, the milling cutter with few edges and coarse teeth should be selected for heavy and rough cutting; For fine and finish machining, the milling cutter with more edges and finer teeth should be selected.
The above is an explanation of the geometric parameters of the tool. Welcome to discuss it together.