Mold costs depe…
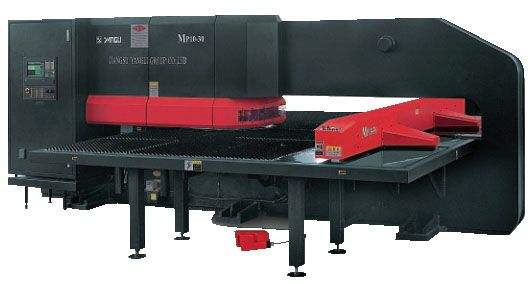
Application of modern NC machining technology in sheet metal machining
With the increasing maturity of microelectronics and computer technology, the development of numerical control technology in China has been promoted. Domestic numerical control systems have been successfully developed, which ensures the quality and performance of numerical control machine tools in China. Because CNC machine tools have the characteristics of strong adaptability to workpiece modification, high machining precision and improving productivity, they have been popularized and applied in various fields.
Numerical control technology has been widely used in sheet metal machine tools. It solves the problems of high precision, complex shape and large batch in sheet metal processing. CNC sheet metal machine tools include CNC shearing machine, CNC laser cutting machine, CNC punch, CNC bending machine, welding machine, flame cutting machine, etc. Their application in production greatly improves the sheet metal processing capacity, ensures the quality and output of sheet metal parts, and greatly reduces the labor intensity of workers.
Shearing and blanking is the first process in the sheet metal processing process. The accuracy of blanking directly affects the processing quality of subsequent processes. The application of NC shearing machine ensures the size of blanking and the work difference of blanking diagonal. Numerical control plate shearing machine is composed of numerical control device, servo system, measuring device and machine tool. The servo system is composed of three servo motors and servo driving devices. There are two servo motors positioned in front of the machine tool. Usually, one main motor works alone, and the processing range is 2-500mm. If the bevel is processed, the auxiliary motor works. The NC system gives two different commands to form the bevel. There is a servo motor in the rear positioning, which mainly processes the products with large board surface, and the processing range is 150 ~ 4000mm. For example, QC12K series CNC plate shears made in Shanghai are equipped with Swiss cyberec dnc60 series, which can store 36 sequences and 100 sequences of internal memory.
S stamping is an important part of sheet metal processing. CNC punch can replace the processing capacity of the past three punch presses. Greatly improved productivity. CNC punch is a machine tool with a wide range of uses, including single punch and turret. Taking cnc1000 as an example, this machine tool is made in Italy. Machine tool with C-type structure, processing range: 1270 × 1000mm, the turret has 19 die stations, which are divided into upper and lower parts to install the punch and die respectively. The external dimensions of the die are 25.4mm, 47.62mm, 88.9mm, 125.43mm, 158.4mm and 210.00mm. The CNC punch generally has three axes of X, y and Z. The x-axis is the 0-degree direction of the machine tool, the y-axis is the 90 degree direction of the machine tool, and the z-axis is installed on the turret, which is the device to control the die angle.
The machine operator shall determine the processing scheme and prepare the program sheet according to the part drawing and process requirements. The operator directly writes the program into the program memory in the edit mode through the operation panel of the machine tool; With the development of CAD / CAM and CIMS technology, operators can input graphics into the computer through computer related software to generate programs, copy them into disk, and input them into the NC system through disk driver. It can also be input by serial method between computer and NC system. The programming instructions of NC punch press are divided into G code and M code. G code is used to instruct the machine tool to carry out machining movement and interpolation mode. Such as G91 increment command, G90 absolute command, g29 arc punching and g68 step circular arc punching. M code is the code that instructs the machine tool to do some auxiliary actions. If M30 program stops. After checking that the procedure is correct, loosen the caliper, put in the workpiece and close the caliper. Start the oil pump and punch to complete the processing.
The CNC punch has the following characteristics:
(1) . automatic centralized lubrication;
(2) Automatic cooling and lubrication of punch die
(3) Screen display and automatic reset of hydraulic overload protector;
(4) Equipped with pneumatic / hydraulic operated variable pressure plate clamp;
(5) Large worktable that can fully support large sheet metal;
(6) Hydraulic numerical control punch with high accuracy, high speed and low noise;
(7) Sliding worktable capable of simple mold replacement and safe interlocking;
(8) Polyurethane free ball device to prevent scratch on the material surface.
The processing technology of NC punch has the following characteristics:
(1) High machining precision. The work difference of hole edge distance is 0.2mm, and the work difference of hole distance is 0.5mm/m.
(2) Because there are many kinds of molds installed on the turret, the workpiece can be clamped at one time and all processing contents can be completed immediately.
(3) The machine tool can process the workpieces individually or batch process the workpieces with group command g98 to improve the productivity.
The workpiece reaches the bending process after two processes: blanking and stamping. CNC bending machine has incomparable advantages over ordinary machine tools. For example, the origin of casprini is Italy, and the input method of Siemens CNC system is manual programming, (1) the preparation is completed by directly inputting the plate thickness, die number, tensile strength, X-axis size, angle, workpiece length and stroke height through the control panel. (2) For some workpieces with complex shape and high precision requirements, input 2D or 3D graphics, plate thickness and die number through the control panel, and use the function of man-machine dialogue to determine the bending sequence and generate the program. After the program is generated, it is stored in the program slow charging area. If it needs to be used later, it is stored in the memory of the machine tool. If the program needs to be used repeatedly, it should be copied out and backed up through a special disk. The CNC bending machine usually has two drag frames at the front and rear. The CNC system controls the bending angle to determine the lifting height of the drag frame, which reduces the labor intensity of the operator. Ordinary CNC bending machine has two servo motors to drive the x-axis and Y-axis of the machine tool. The detection component adopts grating ruler, inductosyn and encoder, which are usually installed on the lead screw of the machine tool. The detection feedback device converts the displacement of the lead screw into an electrical signal and feeds it back to the numerical control device. If there is an error of 0.02mm with the command value, the lead screw is controlled to make adjustment. The high-performance bending machine is equipped with a motor on both sides of the x-axis, so that the x-axis can process beveled edges. A motor is installed on each shaft to process workpieces with different angles on both sides. A motor is added under the rear baffle so that the rear baffle can move up and down, which is more convenient for operation and processing. The common up moving bending machine causes the bending of the lower die due to the long-term use of the hydraulic system on the machine tool. Therefore, the CNC bending machine installs a set of hydraulic system under the machine tool. When the upper and lower dies work with each other, the system applies force to the lower die to reduce the deformation of the lower die and prolong the service time of the lower die.
Features of CNC bending machine:
(1) After the program is established, it can work automatically or semi automatically. The automatic cycle of the program enables the workpiece to be processed at one time, thus changing the inconvenience of large batch of workpieces and complex processes in semi-automatic processing.
(2) The numerical control system automatically calculates the oil pressure to avoid damage to the machine tool caused by overpressure.
(3) The introduction of, 2D and 3D graphics input function facilitates the processing of complex workpieces and improves the processing efficiency.
(4) The addition of various devices improves the processing technology and reduces the labor intensity of the operator.
With the wide application of sheet metal machinery in aerospace, railway transportation, environmental protection equipment, air conditioning appliances, tobacco machinery, packaging and printing, engineering machinery, textile machinery and many other industries. Sheet metal processing also needs more high-tech workers to operate. Good equipment and excellent employees can produce good products, so that there are more excellent Chinese made products in the world.