Mold costs depe…
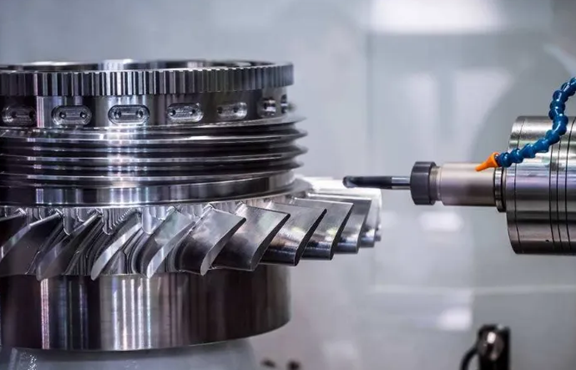
Application analysis of industrial processing laser in mold industry
With the development of science and technology and the diversification of social needs, the competition of products is becoming more and more fierce, and the renewal cycle is becoming shorter and shorter. Therefore, it is required not only to design new products as soon as possible according to the requirements of the market, but also to manufacture prototypes in the shortest possible time, so as to carry out performance testing and modification, and finally form finalized products. In the traditional manufacturing system, it needs a lot of mold design, manufacturing and debugging, which has high cost and long cycle, and can not adapt to the changing market. In order to improve the speed of R & D and production, make high-quality and low-cost molds and products quickly and accurately, and make an agile response to market changes, people have done a lot of research and exploration work. With the continuous decline of industrial laser price and the increasing maturity of industrial laser processing technology, great changes have been brought to mold manufacturing and product production technology. This paper first introduces the industrial processing laser, and then introduces and analyzes several aspects, such as mold laser manufacturing, mold surface laser strengthening and replacement, mold laser repair, mold laser cleaning and so on.
Industrial processing laser
At present, there are two main types of industrial lasers used in laser processing: solid-state lasers and gas lasers. Among them, the solid-state laser is represented by Nd: YAG laser; The gas laser is represented by CO2 laser. With the development of laser technology, high-power fiber lasers and high-power semiconductor lasers are also used in some processing applications.
1) , Nd: YAG laser
The working material of Nd: YAG laser is solid Nd: YAG rod, and its laser wavelength is 1.06 μ m。 Due to the low laser conversion efficiency and the limitation of YAG rod volume and thermal conductivity, the average laser output power is not high. However, because Nd: YAG laser can compress the pulse width of laser output through Q-switch, it can obtain high peak power (108W) when working in pulse mode, which is suitable for laser processing applications requiring peak power; Another advantage is that it can be transmitted through optical fiber, which avoids the design and manufacture of complex transmission optical path. It is very useful in three-dimensional processing. In addition, the laser wavelength can be converted to 355nm (UV) by frequency tripler technology, which can be applied in laser stereo forming technology.
2) CO2 laser
The laser working material of CO2 laser is CO2 mixed gas, and its main application laser wavelength is 10.6 μ m。 Because the laser conversion efficiency of this kind of laser is high, and the heat generated by the laser can be quickly transferred outside the laser gain area through convection or diffusion, the average laser output power can reach a high level (above 10000 watts), meeting the requirements of high-power laser processing.
High power CO2 lasers used in laser processing at home and abroad are mainly cross flow and axial flow lasers. ① Crossflow laser: the beam quality of crossflow laser is not very good. It is multi-mode output and is mainly used for heat treatment and welding. At present, China has been able to produce various high-power cross flow CO2 laser series, which can meet the needs of domestic laser heat treatment and welding. ② Axial flow laser: the beam quality of axial flow laser is good, which is the output of basic mode or quasi basic mode. It is mainly used for laser cutting and welding. The market of laser cutting equipment in China is mainly occupied by foreign axial flow lasers. Although domestic laser manufacturers have done a lot of work on foreign axial-flow lasers, because the main accessories still need to be imported, the product price is difficult to decline significantly and the penetration rate is low.
Wuhan Bolai Technology Development Co., Ltd. has developed a swirling CO2 laser, as shown in Figure 1. With a new rotating gas flow mode, the swirling CO2 laser has the advantages of good beam quality of axial flow CO2 laser and low cost and small volume of cross flow CO2 laser. The popularization and application of this kind of industrial processing laser will play a positive role in promoting the development and popularization of laser processing industry in China.
Mould laser manufacturing
1) Laser indirect molding process
① Stereo lithography apparatus (SLA) process is to form three-dimensional solid workpiece by scanning light curing adhesive layer by layer with ultraviolet laser beam. In 1986, American 3D systems company launched the commercialized prototype sla-1. The highest machining accuracy of SLA process can reach 0.05mm.
② The laminated object manufacturing (LOM) process uses sheet materials, such as paper and plastic film, which was successfully developed by American helisys company in 1986. Through repeated CO2 laser cutting and material pasting, the solid workpiece manufactured in layers is obtained. LOM Process is suitable for manufacturing large workpieces with an accuracy of 0.1mm.
③ Selective laser sintering (SLS) process is formed by powder materials. It was successfully developed by the University of Texas at Austin in in 1989. Three dimensional workpieces are formed by selectively scanning the sintered material powder layer by layer with high-intensity CO2 laser. The biggest advantage of SLS process is that it has a wide range of materials.
The above three laser rapid prototyping technologies have been widely used at home and abroad because of their long development time and relatively mature technology. However, the three-dimensional workpiece formed by the above method can not be directly used as a mold and needs subsequent treatment, so it is called laser indirect molding process. The main processing methods are as follows: ① the rapid prototyping workpiece is used as a die after processing. The paper mold made by LOM directly replaces the sand casting wood mold after surface treatment; Or the paper mold made of LOM can be directly used as low melting point alloy mold and injection mold after surface treatment; Or the forming die of wax mold in wax loss casting. The workpiece made by SLS is used as a metal die after copper infiltration. ② The rapid prototyping part is used as the master mold, and the soft mold is made by pouring silicone rubber, epoxy resin, polyurethane and other materials. ③ Turn over the hard die with rapid prototyping parts. One is to directly use LOM to make paper-based mold, and then grind it into metal mold after surface metal arc spraying and polishing; The other is metal surface hard backing die. The above hard molds can be used for sand casting, die making of EPC, injection mold and simple non steel drawing mold.
The above laser indirect molding process can not only avoid complex mechanical cutting, but also ensure the accuracy of the mold, but also greatly shorten the molding time and save the molding cost. For the precision mold with complex shape, its advantages are particularly prominent. However, at present, there is still the disadvantage of relatively short die life, so the above laser indirect forming die is more suitable for small batch production.
2) Laser direct molding process
Selective laser melting (SLM) technology is developed on the basis of selective laser sintering (SLS) technology. The characteristics of SLM are as follows: (1) using laser beam with high power density and small spot to process metal, so that the metal parts have a dimensional accuracy of 0.1mm; (2) The parts made of molten metal have the entity of metallurgical combination, and the relative density can almost reach 100%, which greatly improves the performance of metal parts; (3) Because the laser spot diameter is very small, it can melt the metal with high melting point with low power, which makes it possible to manufacture parts with single component metal powder. Figure 2 shows all metal parts manufactured by German EOS GmbH using selective laser melting (SLM) process.
Laser multilayer (or three-dimensional / three-dimensional) cladding direct rapid prototyping technology is a high-tech manufacturing technology developed on the basis of rapid prototyping technology and synchronous feeding laser cladding technology. Its essence is three-dimensional laser cladding under computer control. Due to the rapid solidification characteristics of laser cladding, the fabricated metal parts have uniform and fine dendrite structure and excellent quality, and their density and properties are equivalent to those of conventional metal parts. Laser multilayer cladding has developed a variety of methods, among which the most representative is the rapid prototyping technology of metal parts called laser engineered net shaping (lens) developed by Sandia National Laboratories. Stainless steel, maraging steel, nickel base superalloy, tool steel, titanium alloy, magnetic material and nickel aluminum intermetallic compound workpieces have been successfully manufactured by this method, and the density of the parts is nearly 100%. Figure 3 shows the metal mold manufactured by Sandia National Laboratory with lens technology.
Selective laser melting (SLM) technology and laser engineering net forming (lens) technology have been widely valued by the industrial and academic circles because of their good compactness, high metallurgical bonding structure and precision, and long service life. A variety of equipment prototypes have been introduced abroad, and some have even begun to be commercialized; At present, the research and application in China is still in its infancy.
In addition, there is a layered manufacturing technology (LOM) of metal parts based on laser fine cutting, which can manufacture large and complex molds quickly and at low cost. Japan’s Nakagawa Weixiong research laboratory applied the sheet metal LOM technology to realize the layered rapid manufacturing of metal molds as early as the 1980s. After development, sheet metal LOM technology has been gradually applied to the manufacture of large interior and exterior decoration molds such as automobiles and injection molds with complex flow channels.
Laser modification of die surface
Mold surface treatment has always been an important issue in the field of machining. With the development of new technology and new process, many traditional treatment methods are not suitable. For the mold with complex shape, the most ideal surface treatment method is to use laser. It has almost no deformation. The surface hardness is higher than that of the conventional treatment method, and it is more wear-resistant and has a longer service life.
1) Laser transformation hardening
Laser transformation hardening is also called laser quenching. Because the cooling rate of laser quenching is much higher than that of conventional quenching, very fine martensite can be obtained. Laser transformation hardening has the advantages of higher hardness than conventional quenching, less deformation, thin surface layer and local quenching, and does not affect the mechanical properties of the substrate.
2) Laser shock strengthening
Laser shock strengthening is a technology that changes the physical and mechanical properties of material surface by strong shock wave generated by the interaction between high power density and short pulse laser beam and material. In the process of laser shock, because the peak stress of shock wave induced by laser is greater than the dynamic yield stress of the material, the material produces dense, uniform and stable dislocation structure, makes the metal surface plastic deformation and forms deep residual compressive stress, so as to improve the strength, wear resistance, corrosion resistance and fatigue life of metal parts. Its main advantages are: high impact pressure, and the strengthening depth reaches 4 ~ 8 times of the traditional shot peening strengthening depth; It can process parts that cannot be processed by traditional technology, such as small grooves, small holes and contour lines; The metal surface strengthened by laser shock will not produce distortion, mechanical damage, thermal stress damage and phase transformation.
3) Laser alloying and laser cladding
Laser alloying and laser cladding is to coat a layer of material with certain properties different from the mold matrix, and irradiate the coating area with high-energy laser beam at the same time. Laser alloying causes the coating material to melt together with part of the substrate and produce alloying process by adjusting the laser output power; Laser cladding is the rapid combination of the coating layer and the substrate surface under the action of laser. The main difference between it and laser alloying is that the chemical composition of the coating basically does not change after the action of laser, and the composition of the substrate basically does not enter the coating. The new technology of laser surface alloying and laser cladding surface modification based on the synthesis and preparation of rapid solidification new materials is one of the most effective methods to improve the wear and corrosion resistance of die materials at high temperature.
Two, mold laser repair
In fact, the failure of the die is scrapped due to the wear of local materials on the surface, and the processing cycle of the metal die is long and the processing cost is high. The service life of the die depends on its ability to resist wear and mechanical damage. Once it is excessively worn or mechanically damaged, it must be repaired before it can be restored to use. At present, the commonly used maintenance technologies include electroplating, surfacing and thermal spraying. The electrodeposited layer is thin, and the combination with the substrate is poor, and the damaged part of the shape is difficult to repair; During surfacing and spraying, the heat injection is large and the heat affected zone of the die is large. The application of laser for mold maintenance, due to the approximate adiabatic rapid heating caused by the high energy density of laser beam, has little thermal impact on the matrix, and the distortion caused can be ignored. There are two main methods for laser repair of molds:
1) Repair of laser cladding die
The repair of the die is realized by laser cladding. The high-power CO2 laser beam is incident on the die surface at the same time with the metal powder flow at a constant power. The metal melts to produce a molten pool, and then solidifies rapidly to form a metallurgically bonded coating. This method generally uses high-power CO2 laser as the heat source, which is suitable for the repair of molds with large volume and large wear area, as well as the repair of large workpieces such as steel rolls.
2) Repair of laser deposition welding die
The repair of laser deposition welding die adopts medium and small power pulsed Nd: YAG laser, and the defects of the die are filled with laser beam and filamentous filling material. The laser beam melts the welding wire and the surface of the workpiece at the same time, and the required sediment height is achieved by multi-layer welding; After welding, the mold parts are processed into the final size. This method is suitable for precision molds with small volume. Starweld welding machine manufactured by rofin Sinar company is a representative of this kind of equipment.
The application of high-energy laser pulse to remove the surface dirt produced in the process of mold use is another application of laser technology in the mold industry. There are two cleaning mechanisms: one is to directly use laser to heat the dirt to make it vaporize and volatilize, or instantly heat and expand and be taken away from the surface of the mold substrate by steam; In addition, under the action of high-energy density and high-frequency pulsed laser, the split stress is generated in the dirt layer, which is separated from the mold matrix. Compared with the traditional sand blasting cleaning method, laser cleaning has the advantages of fast cleaning speed, no damage to the mold surface and on-line cleaning (which can save a lot of disassembly, installation and commissioning time). At present, the laser cleaning equipment produced by German jet laser system company is relatively advanced.
Concluding remarks
The high brightness, high directivity and high monochromaticity of the laser make the laser beam focus through the lens, which can produce a high temperature of thousands or even tens of thousands of degrees near the focus, which makes it possible to process almost all materials. Laser processing has been widely used in various manufacturing fields and industries abroad; At the same time, China has been investing a lot of manpower and material resources in the research and development of laser processing equipment and laser processing technology. Mold is one of the important industrial equipment for industrial product forming, which determines the adaptability of enterprises in market competition to a great extent. Mold forming has become an important means and process development direction of modern industrial products. Laser processing has great advantages in die manufacturing and replacing die in some occasions (such as laser cutting replacing punching die in sheet metal parts and laser marking replacing punching die marking). How to apply laser processing technology to shorten mold manufacturing cycle (T), ensure mold manufacturing quality (q) and reduce mold manufacturing cost (c) in actual production needs continuous in-depth research and exploration.