Mold costs depe…
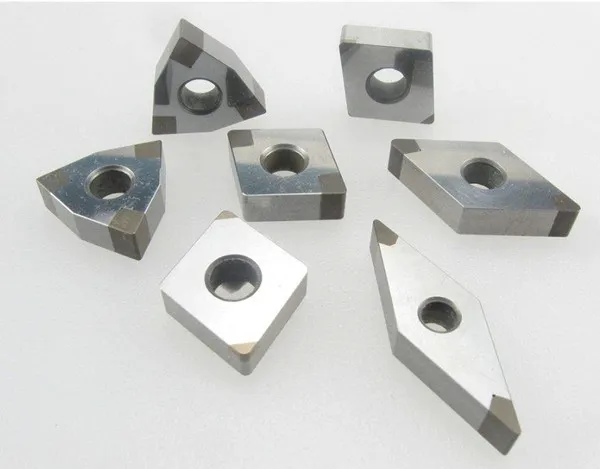
Analysis of PCD and PCBN Cutting Tools
With the advent of modern integrated manufacturing system and the continuous improvement of cutting speed, machining is developing in the direction of high speed, compound, intelligent and environment-friendly, which puts forward higher requirements for tool performance. It is an inevitable trend to develop a variety of super hard cutting tools with excellent wear resistance that can be stably processed for a long time. Cutting tools are gradually developing towards efficient machining, hard machining, dry machining, ultra precision machining and machining of new difficult to machine materials. PCD tools and PCBN tools are necessary machining tools to achieve precision and ultra precision machining.
In the past, PCD/PCBN tools were hardly used in actual machining unless they were indispensable for special machining. Because PCD/PCBN tool cost is too high.
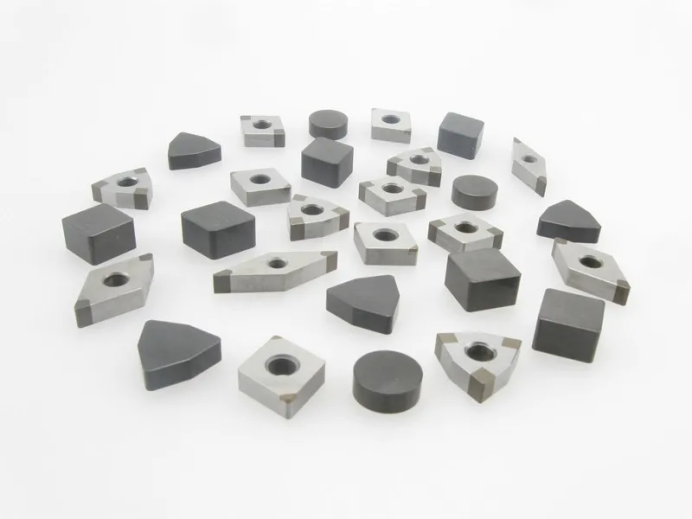
Nowadays, although PCD/PCBN tools are still a little expensive, their quality and reliability have been improved. Thus, PCD/PCBN tools have strong competitiveness in many mechanical processing in the automotive, aerospace, medical equipment and other industrial fields. When PCD/PCBN tools are installed on machine tools and tool holders with good rigidity, manufacturers can make full use of the potential of PCD/PCBN to improve productivity. At the same time, in various machining applications, PCD/PCBN tools provide manufacturers with greater choice of cutting tools. It gives them more favorable opportunities to improve cost and productivity.
PCD/PCBN knives have three basic forms: integral type, full section type and tip type. The new PCBN integral tool with larger size and thicker thickness has good wear resistance and impact resistance. The good wear resistance and impact resistance of cutting tools are the key means for processing cast iron materials containing less than 10% ferrite. The improvement of tool wear resistance and impact resistance is also particularly important for processing alloy cast iron parts in the automobile industry. In the past, this kind of alloy cast iron parts could only be finished by grinding.
When roughing alloy cast iron, the tool must undergo intermittent cutting caused by surface cracks, residual sand and other original surface discontinuities left by the casting process. Good wear resistance also plays a great role in finishing, especially for workpieces with chromium content of 28%~30% and hardness of 68~70HRC.
The overall PCBN blade has multiple cutting edges on both sides, thus reducing the tool cost of unit production parts. Its cross section is 4.76 mm thick, which is 3.17 mm thicker than the traditional tool. This allows the blade to be reliably installed on the standard gasket cemented carbide handle groove. WeChat of metal processing has good content and deserves attention.
PCBN blades are also made into full section and knife point shapes. The full face blade has a complete PCBN top surface, which is sintered on a cemented carbide substrate. It only provides multiple cutting edges on one side of the blade. This blade is cheaper than the whole blade. A PCBN blade is welded on a corner of the cemented carbide substrate. The tool tip is either a single cutting edge or a double cutting edge. Most PCBN blades used today are knife point shaped. Both full section and pointed blades are manufactured according to the industrial standard size. Like the integral blade, they can be installed in the blade groove of the standard cutter bar and on the milling cutter groove.
PCBN tool is more suitable for machining hard parts
The tools made of PCBN are most suitable for cutting hard parts. In fact, the lower limit of hardness of machined parts is 45HRC. If PCBN tool is used to machine parts with hardness lower than 45HRC, tool marks will be generated.
In rough machining, the maximum cutting depth of white iron and other hard high chromium iron is about 4.76 mm, the maximum cutting depth of unalloyed pure cast iron is 6.4 mm, and the cutting speed of finish machining varies from 107~122 m/min for processing high chromium iron to 2134 m/min for processing gray cast iron. All machining with PCBN tools requires the use of very rigid tools, fixtures, spindles and machine tools.
The cutting speed of proper PCBN tool finishing varies significantly with the workpiece material, material height and the size and shape of the part. For example, when machining hardened steel with Rockwell hardness of 60 ~ 62HRC, you can reach the cutting speed of 183m/min with a cutting depth of 0.51mm; Feed rate is 0.05~O 1mm/r can produce lower surface roughness; The harder the material is, the higher the cutting speed is required. However, when the cutting speed is greater than about 198m/min, excessive wear will occur. Very high cutting speed can be used to process ordinary cast iron.
Pointed PCBN tools are both economical and reliable for rough machining and finishing. However, in this case, it is required to use integral tools and full section tools. A typical example is the rough boring of the middle part of the cylinder liner with casting burrs. When machining with a sharp tool at a very accurate cutting depth, the burrs on the workpiece can eventually make the PCBN blade deviate from the correct position. Powerful overall and full face PCBN tools can eliminate such problems. Both integral and full face tools can be reground, thus prolonging tool life and compensating for their higher costs. In order to obtain the best cost-effectiveness of the integrated tool, the cutting edges on both sides of the integrated tool should be used.
At present, the biggest development field of PCBN tools is high hard cutting – finishing of alloy steel parts of automobile engines such as gears, shafts and bearings with Rockwell hardness of 60~65HRC. From the traditional point of view, such parts can only be made after grinding. Moreover, the dimensional tolerance of parts is very small, and the surface roughness is very fine. The high hard cutting makes the same result possible on a CNC lathe, and the price is only half of the cost of machining parts with the same machining quality on a CNC grinder. In addition, the maintenance cost of the lathe is low.
Because the cutting depth of high hard cutting is only 0.3~0.38mm, low cost PCBN tool tip can be used.
The test results of American Advanced Carboloy Materials Company show that the surface roughness of hardened steel parts (60 ~ 62HRC) can be 0.2 µ m or less by continuous machining with knife point PCBN.
Dry cutting with PCBN tool
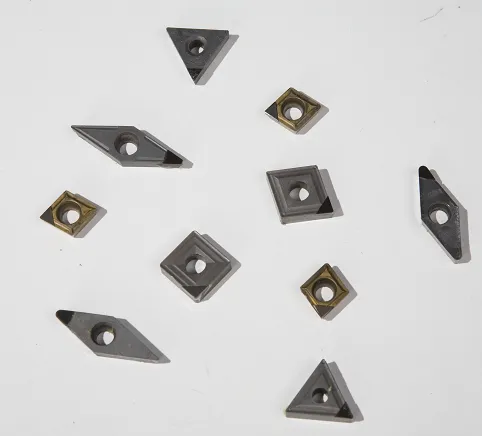
Although the PCBN tool has enough hardness to resist the deformation caused by cutting heat during cutting, it is very brittle. If coolant is added, the tool edge is prone to crack due to sudden temperature drop. Therefore, when PCBN tool is used to process parts, dry cutting is generally required, especially in the case of intermittent cutting, and coolant must not be used. The quality of tool grinding has a great influence on the success of PCBN tool machining. In order to prolong the tool life, proper tool grinding methods must be used to strengthen the cutting edge of the tool. PCBN tool grinding varies with the machining materials and rough and finish machining. When finishing cast iron, the tool grinding amount is small, while when roughing white iron, it is necessary to grind a 3.8mm wide T-shaped blade edge with 15 °. You can also use the method of combining the edge of the blade with the fine grinding. Add a cutting edge edge on the tool to strengthen the cutting edge strength. For example, add a 20 ° edge to a 90 ° tool angle to obtain a 110 ° tool angle. The larger the angle, the better the cutting edge strength.
Since the cutting edge of the strengthened PCBN tool changes the direction of cutting force away from the cutting edge, it is generally necessary to keep the spindle surface of the cutting edge corresponding to the hardness of the workpiece material. During rough machining of cast iron, the T-shaped blade edge is about 0.2mm wide, 20 °; When finishing cast iron, only a slight grinding amount is required. When machining steel with hardness of 65RC, the width of T-shaped edge surface of the tool shall be 0.1~0.2mm and the angle shall be 20 °.
Processing nonferrous alloys with PCD tools
Now, the majority of production users have overcome the shock of the blade tip. They found that PCD tools are cost-effective. PCD tools are obviously superior to cemented carbide tools in the processing of most non-ferrous metals, which is not due to any development of processing materials. WeChat of metal processing has good content and deserves attention.
At present, most PCD tools are sharp. A PCD blade is welded to a corner of the carbide tool holder. PCD cutter block size has been standardized in industry, and can be used in the cutter groove of standard cutter bar and milling cutter groove. Unlike cemented carbide tools, PCD tools cannot be indexed, and only have a single blade.
The full section PCD tool with standard size has a complete PCD top surface, which is sintered on the cemented carbide substrate. Although the full section tool is expensive at the beginning, it is indexable and can provide multiple cutting edges on one side of the tool. When purchasing, this kind of knife is usually round, so as to get the most blades. At first, full section PCD tools were mainly used in special occasions.
Safe and reliable blade retention plays a key role in the application of PCP tools, especially for rotary tools, wedge and screw are now used together, just like conical tools and wedges, to improve the fixation of tools. Common thread and press plate design. The necessary rigidity can be provided by the tool with suspended cutter bar and PCD blade directly welded on the cutter bar. The tool device with good rigidity can provide more reliable PCD tools.
Solid work-piece clamps, machine tools and spindles with good rigidity can also improve processing characteristics. Today’s CNC lathes and machining centers have the rigidity required by PCD/PCBN cutting tools. When installing new equipment, the environment of the machining workshop must be considered to make the environment more suitable for high-performance PCD/PCBN cutting tools.
The tool for precision milling aluminum automobile conduit is usually used by combining the tip PCD tool with the common carbide tool to cut the casting burrs encountered at a certain cutting depth. These casting burrs are easy to continuously impact the solder joint between PCD blade and cemented carbide tool body, and finally make PCD blade shift.
PCD tip tool can be used for milling at the maximum cutting depth of about 60% of the length of PCD blade. The burr can still make the PCD blade shift on the tool even if the machining is conducted at or below the maximum cutting depth. This problem can be solved by adding some common carbide inserts to the milling cutter. The cemented carbide inserts installed on the milling cutter shall be slightly adjusted in the axial and radial directions of the milling cutter. In this way, the carbide tool can cut off the burrs in front of the PCD cutter, and do a good job of pre processing for the finishing of the PCD cutter. Another important application of tip PCD tools is to finish machining automotive parts in the so-called “three-dimensional” process. In order to save freight and facilitate the collection of chips such as rough aluminum cylinder heads, the foundry is used for recycling. They use a PCD cutting tool to semi finish the castings, including the top, bottom, side and edge of the castings, with a very high metal removal rate. The machined mechanical parts are rectangular and easy to load, unload and pack. As the parts occupy less space, the freight rate of the cargo ship decreases.
Manufacturers should improve productivity, carry out continuous machining of parts, and extend tool life (eliminate frequent tool changes). When using PCD tip cutter, it can tilt a little on the cemented carbide. PCD tools are better than grinding when machining high silicon aluminum automobile parts, such as cylinder head, engine block, conduit, gearbox and wheel.
When machining with PCD tools, effective chip removal is very important. PCD tools produce chips very quickly. The machining system must remove chips from the working area continuously and quickly. Coolant, air mist, chilled air and their combination will have an impact. The cutting speed of PCD tool is up to 3048m/min, which requires an effective chip removal device and a rigid machine tool and operating system. Now CNC machine tools and machining centers can easily reach this speed.