Mold costs depe…
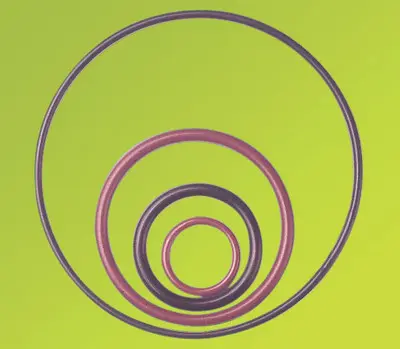
Main Failure Causes of O-ring and Its Preventive Measures
Improper design and use of O-ring will accelerate its damage and lose its sealing performance. The experiment shows that if each part of the sealing device is reasonably designed and the pressure is simply increased, the O-ring will not be damaged. Under the working conditions of high pressure and high temperature, the main reasons for O-ring damage are the permanent deformation of O-ring materials and the gap bite caused by O-ring being squeezed into the sealing gap. The primary O-ring appears distorted during movement.
1. Permanent deformation
Because the synthetic rubber material used for O-ring seal ring is viscoelastic material, the initially set compression amount and rebound blocking capacity will be gradually lost after long-term use, resulting in permanent deformation and eventually leakage. Permanent deformation and loss of elastic force are the main reasons for loss of sealing performance of O-ring. The following are the main reasons for permanent deformation.
1) Relationship between permanent deformation and compression ratio and tensile amount
The rubber of various formulas used for making O-ring will produce the phenomenon of compression stress relaxation under compression, at this time, the compression stress will decrease with the increase of time. The longer the service time, the greater the compression ratio and the tensile amount, the greater the stress drop caused by the rubber stress relaxation, so that the O-ring has insufficient elasticity and lost its sealing capacity. Therefore, it is advisable to try to reduce the compression ratio under the allowable use conditions. Increasing the section size of the O-ring is the simplest way to reduce the compression ratio, but it will increase the structure size.
It should be noted that when calculating the compression ratio, people often neglect the reduction of the section height caused by the stretching of the O-ring during assembly. The change of the cross section area of the O-ring is inversely proportional to the change of its circumference. At the same time, due to the effect of tension, the section shape of the O-ring will also change, which is shown by the reduction of its height. In addition, under the effect of surface tension, the outer surface of the O-ring becomes flatter, that is, the section height decreases slightly. This is also a manifestation of compression stress relaxation of O-ring seals.
The deformation degree of the O-ring section also depends on the hardness of the O-ring material. In the case of the same tensile amount, the section height of the O-ring with high hardness also decreases a lot. From this point of view, the material with low hardness should be selected as far as possible according to the service conditions. Under the action of liquid pressure and tension, the rubber O-ring will also gradually undergo plastic deformation, and its section height will be reduced accordingly, so that the sealing capacity will eventually be lost.
2) Relationship between Temperature and O-Ring Relaxation Process
The service temperature is another important factor affecting the permanent deformation of the O-ring. High temperature will accelerate the aging of rubber materials. The higher the operating temperature, the greater the compression permanent deformation of the O-ring. When the permanent deformation is greater than 40%, the O-ring will lose its sealing capacity and leak. The initial stress value formed in the rubber material of the O-ring due to compression deformation will gradually decrease and disappear with the relaxation process of the O-ring and the effect of temperature drop. The initial compression of O-ring working under zero temperature may decrease or disappear completely due to the sharp drop of temperature. Under the condition of – 50~- 60 ℃, the rubber material that is not resistant to low temperature will completely lose the initial stress; Even for low temperature resistant rubber materials, the initial stress at this time will not be greater than 25% of the initial stress at 20 ℃. This is because the initial compression of the O-ring depends on the linear expansion coefficient. Therefore, when selecting the initial compression amount, it is necessary to ensure that there is still enough sealing capacity after the stress drop caused by the relaxation process and temperature drop.
For O-rings operating under zero temperature, special attention shall be paid to the recovery index and deformation index of rubber materials.
To sum up, in the design, it is necessary to ensure that the O-ring has a suitable working temperature, or select the O-ring materials that can withstand high and low temperatures to extend the service life.
3) Medium working pressure and permanent deformation
The pressure of the working medium is the main factor causing the permanent deformation of the O-ring. The working pressure of modern hydraulic equipment is increasing. The O-ring will be permanently deformed under high pressure for a long time. Therefore, appropriate pressure resistant rubber materials shall be selected according to the working pressure during design. The higher the working pressure, the higher the hardness and high pressure resistance of the materials used.
In order to improve the pressure resistance of O-ring materials, increase the elasticity of materials (especially the elasticity of materials at low temperatures), and reduce the compression permanent deformation of materials, it is generally necessary to improve the formula of materials and add plasticizers. However, if the O-ring with plasticizer is immersed in the working medium for a long time, the plasticizer will gradually be absorbed by the working medium, resulting in the volume shrinkage of the O-ring, and even negative compression of the O-ring (that is, there is a gap between the O-ring and the surface of the sealed part). Therefore, these shrinkage should be fully considered when calculating the compression of the O-ring and designing the die. The pressed O-ring shall be able to maintain the necessary size after being immersed in the working medium for 5~10 days and nights.
The compression permanent deformation rate of O-ring material is related to temperature. When the deformation rate is 40% or more, leakage will occur. Therefore, the heat resistance limits of several rubber compounds are: nitrile rubber 70 ℃, ethylene propylene diene monomer 100 ℃, fluororubber 140 ℃. Therefore, various countries have stipulated the permanent deformation of O-ring. See the table for the size changes of O-rings of Chinese standard rubber materials at different temperatures. Under the same temperature, the compression permanent deformation rate of O-rings with large section diameter is lower.
The situation is different in oil. Since the O-ring is not in contact with oxygen at this time, the above adverse reactions are greatly reduced. In addition, it usually causes a certain expansion of the rubber, so the compression permanent deformation rate caused by temperature will be offset. Therefore, the heat resistance in oil is greatly improved. Take nitrile rubber as an example, its working temperature can reach 120 ℃ or higher.
2. Intermittent bite
The sealed parts have poor geometric accuracy (including roundness, ovality, cylindricity, coaxiality, etc.), misalignment between parts, and internal diameter expansion under high pressure, which will cause the expansion of sealing clearance and intensification of clearance extrusion. The hardness of O-ring also has an obvious effect on the phenomenon of gap extrusion. The higher the pressure of liquid or gas is, the smaller the hardness of O-ring material is, and the more serious the gap extrusion of O-ring is.
The measure to prevent clearance bite is to strictly control the hardness of the O-ring and the sealing clearance. Select sealing materials with proper hardness to control the clearance. The hardness range of commonly used O-rings is HS60~90. Low hardness is used for low pressure, and high hardness is used for high pressure.
It is an effective way to prevent the O-ring from being squeezed into the clearance by using a proper sealing ring to protect the retaining ring.
3. Distortion phenomenon
Twist refers to the phenomenon that the O-ring twists in the circumferential direction, which generally occurs in the dynamic seal state.
If the O-ring is properly assembled and used under appropriate conditions, it is not easy to roll or twist under reciprocating motion, because the contact area between the O-ring and the groove is larger than the friction contact area on the sliding surface, and the resistance of the O-ring itself can prevent twisting. The distribution of friction also tends to keep the O-ring stationary in its groove, because the static friction is greater than the sliding friction, and the roughness of the groove surface is generally inferior to the roughness of the sliding surface.
There are many reasons for distortion damage, among which the most important is that the gap between the piston, piston rod and cylinder barrel is uneven, the eccentricity is too large, and the section diameter of the O-ring is uneven. Because the friction force on the O-ring is uneven for more than one week, some parts of the O-ring have too much friction, causing distortion. Generally, O-ring with small section size is prone to uneven friction. Cause distortion (This is why the section diameter of the O-ring for movement is larger than that of the O-ring for fixation.)
In addition, due to the coaxiality deviation, unequal sealing height and uneven section diameter of the O-ring in the sealing groove, one part of the O-ring may be compressed too much, and the other part may be too small or not compressed. When the groove is eccentric, that is, the coaxial deviation is greater than the compression amount of the O-ring, the seal will completely fail. Another disadvantage of large coaxiality deviation of sealing groove is uneven compression of O-ring along the circumference. In addition, due to the uneven section diameter, material hardness, lubricating oil film thickness, etc. of the O-ring, as well as the roughness of the seal shaft surface and other factors, part of the O-ring slides along the working surface and the other part rolls, resulting in the distortion of the O-ring. The O-ring for sports is easily damaged due to twisting, which is an important reason for the damage and leakage of the sealing device. Therefore, improving the machining precision of the seal groove and reducing the eccentricity are important factors to ensure the reliable sealing and life of the O-ring.
The sealing ring should not be installed in a twisted state. If it is distorted during installation, the distortion damage will occur quickly. In operation, the distortion will cut off the O-ring, resulting in a large amount of oil leakage, and the cut O-ring will mix with other parts of the hydraulic system, causing serious accidents.
In order to prevent the O-ring from being twisted and damaged, the following points should be noted during design
1) The concentricity of the O-ring installation groove should be considered from two aspects: easy processing and no distortion.
2) The section size of O-ring shall be uniform, and the sealing part shall be fully coated with lubricating oil or grease during each installation. Sometimes, felt ring type oil filling device saturated with lubricating oil can also be used.
3) Increase the section diameter of the O-ring, and the section diameter of the O-ring for dynamic seal should generally be larger than that of the O-ring for static seal; In addition, O-rings should not be used as seals for large diameter pistons.
4) When distortion damage also occurs under low pressure, seal ring can be used to protect the retaining ring.
5) Reduce the surface roughness of cylinder barrel and piston rod.
6) The O-ring is made of materials with low friction coefficient.
7) The O-ring can be replaced by a seal ring that is not easy to distort.
4. Abrasive wear phenomenon
When the seal clearance has relative movement, dust and sand particles in the working environment are adhered to the surface of the piston rod, and along with the reciprocating movement of the piston rod, they are brought into the cylinder together with the oil film, becoming abrasive particles invading the surface of the O-ring, accelerating the wear of the O-ring, so that its sealing performance is lost. In order to avoid this, a dust ring must be used at the extended shaft end of the reciprocating sealing device.
5. Influence of sliding surface on O-ring
The roughness of sliding surface is a direct factor affecting the friction and wear of O-ring surface. Generally speaking, the friction and wear of the smooth surface is small, so the roughness value of the sliding surface is often very low (Ra0.2~0.050 μ m)。 However, the test shows that the surface roughness is too low (Ra is below 0.050 μ m) It will also bring adverse effects on friction and wear. This is because the tiny surface is uneven, which can maintain the necessary lubricating oil film. Therefore, appropriate surface requirements shall be selected.
The material of sliding surface also affects the service life of O-ring. The harder the sliding surface material is, the higher the wear resistance is, and the stronger the ability to keep it smooth and clean, and the longer the service life of the O-ring is. This is also an important reason for the chrome plating on the surface of the piston rod of the hydraulic cylinder. Similarly, it can be explained that the sliding surface made of copper and aluminum alloy with the same roughness has more serious friction and wear on the sealing ring than the steel sliding surface, and the sealing ring with low hardness and large compression is not as durable as the sealing ring with high hardness and small compression.
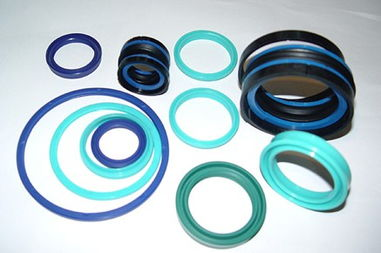
6. Friction and Application of O-ring
In the dynamic sealing device, friction and wear are important factors affecting the damage of O-ring. The degree of wear mainly depends on the size of friction. When the liquid pressure is small, the friction force of O-ring depends on its pre compression. When the working fluid is under pressure, the friction increases with the increase of the working pressure. When the working pressure is less than 20MPa, the relationship is approximately linear. When the pressure is greater than 20MPa, with the increase of the pressure, the contact area between the O-ring and the metal surface increases slowly, and the friction force increases slowly. Under normal conditions, the service life of O-ring will decrease approximately in a square relationship with the increase of liquid pressure.
With the increase of friction, a large amount of friction heat is generated between the rotating or reciprocating shaft and the O-ring. As most O-rings are made of rubber, the thermal conductivity is very poor. Therefore, the friction heat will cause the aging of the rubber, leading to the effectiveness of the O-ring and damaging its sealing performance. Friction will also cause O-ring surface damage, reducing the compression. Serious friction will soon cause the surface of the O-ring to be damaged and lose its sealing property. When the seal is used for pneumatic reciprocating motion, the friction heat will also cause adhesion, which will further increase the friction