Mold costs depe…
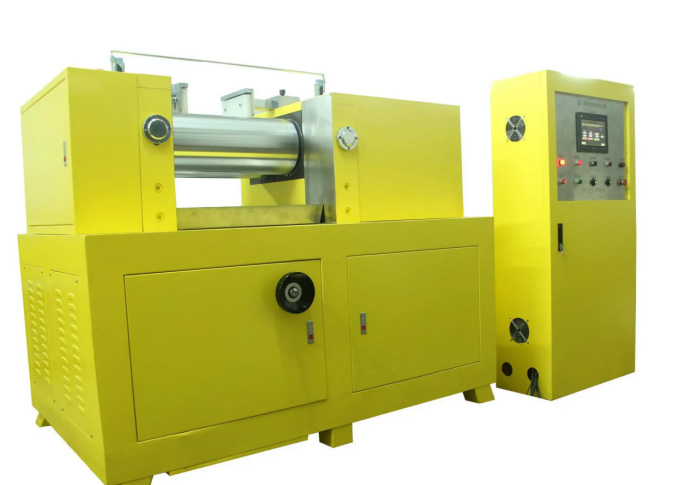
Brief introduction of rubber processing technology
1. Plasticizing mechanism
Rubber is plasticized to increase its plasticity. Its essence is to break rubber molecular chains and reduce the length of macromolecules. Fracture can occur not only in the main chain of macromolecules, but also in the side chain. As rubber is subject to oxygen, electricity, heat, mechanical force, plasticizer and other factors during plasticizing, the plasticizing mechanism is closely related to these factors, among which oxygen and mechanical force play an important role, and they complement each other. Generally, plasticizing can be divided into low-temperature plasticizing and high-temperature plasticizing. The former is dominated by mechanical degradation, and oxygen plays a role in stabilizing free radicals; The latter is dominated by automatic oxidation and degradation, and mechanical action can strengthen the contact between rubber and oxygen.
During plasticizing, the mechanical force of the roller on the raw rubber is very large and forces the rubber molecular chain to break, which mostly occurs in the middle part of the macromolecule.
During plasticizing, the longer the molecular chain is, the easier it is to cut off. One of the important reasons why cis polybutadiene rubber is difficult to break the chain mechanically is the lack of high molecular weight in raw rubber. When high molecular weight fraction is added, remarkable effect can be obtained during low-temperature plasticizing.
Oxygen is an indispensable factor in plastic smelting. When oxygen is lacking, the expected effect cannot be obtained. Raw rubber has been refined
During plasticizing, the friction between equipment and rubber obviously increases the rubber temperature. Heat is very important to the plasticizing effect, and the influence is different in different temperature ranges. As the molecular chain is broken mainly by mechanical force during low-temperature plasticizing, the viscosity of raw rubber decreases with the increase of temperature in the stamp area (natural rubber is lower than 110 ℃). The force applied during plasticizing is small, so that the plasticizing effect decreases instead. On the contrary, oxidation cracking reaction plays a leading role in high temperature plasticizing, so the plasticizing effect will increase with the increase of temperature in high temperature zone (natural rubber is higher than 110 ℃), so temperature plays a role in promoting plasticizing. Due to different properties of various rubbers, the temperature range corresponding to the lowest plasticizing effect is also different, but the curve shape of temperature effect on plasticizing effect is similar. It is known that the use of chemical plasticizers can improve the plasticizing effect no matter at low temperature or high temperature. Acceptor plasticizers, such as benzoquinone and azobenzene, act as free radical acceptors during low-temperature plasticizing, which can stabilize the free radicals of broken rubber molecules and then generate shorter molecules; Initiating plasticizers, such as dibenzoyl peroxide and azodiisobutyronitrile, decompose into extremely unstable free radicals at high temperatures, then trigger rubber molecules to generate macromolecular free radicals, and then oxidative fracture. In addition, such as mercaptans and phthalamido phenyl disulfides, they can not only stabilize the free radicals of rubber molecules, but also trigger the formation of free radicals of rubber under high temperatures to accelerate automatic oxidative fracture. Therefore, these chemical plasticizers are called mixed plasticizers or chain transfer plasticizers.
2. Plasticizing process
Before plasticizing, raw rubber usually needs to be dried, cut, selected and broken. The purpose of baking is to reduce the hardness of raw rubber so that it can be cut, and at the same time, the crystallization can be removed. It is required that the drying temperature is not high, but the time is long, so it should be noted that the physical and mechanical properties of rubber will not be affected; For example, the drying temperature of natural rubber is generally 50~60 ℃, and the drying time takes tens of hours. After the raw rubber is taken out from the drying room, it is cut into large pieces of about 10-20kg. After the impurities are manually removed, the rubber is broken by a rubber breaker for plastic refining.
According to the type of equipment used for plasticizing, plasticizing can be roughly divided into three methods.
1. Open mill plasticizing
Its advantages are good plastic compound quality, small shrinkage, low production efficiency and high labor intensity. This method is suitable for factories with more rubber changes and less rubber consumption.
Plastic smelting by steel mill is a kind of low-temperature plastic smelting. Therefore, reducing the rubber temperature to increase the force is the key to open mill plasticizing. Equipment characteristics and process conditions related to temperature and mechanical action are important factors affecting the plasticizing effect.
In order to reduce the rubber temperature, the roller of the steel mill needs to be effectively cooled. Therefore, the roller is equipped with a water pipe with an eyelet, which directly sprays water on the surface of the roller for cooling to reduce the need for effective cooling of the roller. This can meet the basic requirements for the roller temperature during the plastic refining of various rubber materials. In addition, the method of film cooling is also effective. For example, the film formed by plasticizing can be naturally cooled by air through a long conveyor belt (or guide roller) and then returned to the roller, or thin through plasticizing (reducing the roller pitch to make the film thinner for cooling). The purpose of staged plasticizing is also to reduce the rubber temperature. Its operation is to divide the whole plasticizing process into several sections to complete. After each section of plasticizing, the raw rubber needs to be fully parked for cooling. Plasticizing is generally divided into 2~3 sections, and each section is parked for cooling for 4~8 hours. The rubber temperature increases with the extension of plasticizing time. If it cannot be cooled in time, the plasticity of raw rubber only increases significantly at the initial stage of plasticizing, and then changes little. This phenomenon is caused by the softening of raw rubber due to the increase of temperature, the easy sliding of molecules and the reduction of mechanical degradation efficiency. High glue temperature will also produce false plasticity, which will decrease once it is parked and cooled. The bigger the speed ratio of the two rollers is, the stronger the shearing effect is; Therefore, the better the plasticizing effect is. Reducing the roll spacing can also increase the mechanical shearing effect and improve the plasticizing effect.
2. Internal mixer plasticizing (high temperature, intermittent)
The internal mixer has large production capacity, low labor intensity and low power consumption; However, because it is a closed system, it is difficult to clean, so it is only suitable for the occasions where the rubber grade changes little.
The structure of the internal mixer is complex. On the one hand, the raw rubber in the internal mixer is subject to the shear stress and friction between the rotor and the cavity wall, on the other hand, it is also subject to the external pressure of the top bolt. The heat generated during internal mixing is very high, and the materials cannot be cooled in time. Therefore, it belongs to high temperature plastic mixing. The temperature is usually higher than 120 ℃, or even between 160 ℃ and 180 ℃. According to the above-mentioned high-temperature plasticizing mechanism, the raw rubber in the internal mixer mainly improves the plasticity of rubber by means of strong oxidation chain breaking at high temperature; Therefore, temperature is the key, and the plasticizing effect of internal mixer increases with the increase of temperature. When the natural rubber is plasticized by this method, the temperature generally does not exceed 155 ℃, and 110~120 ℃ is the best. If the temperature is too high, the physical and mechanical properties of the rubber will decline.
3. Plastic refining by screw machine (high temperature, continuous)
Screw plasticizing is characterized by continuous plasticizing at high temperatures. On the one hand, the raw rubber in the screw extruder is strongly stirred, and on the other hand, due to the friction between the raw rubber and the inner wall of the barrel, a large amount of heat is generated, which accelerates the oxidative cracking.
The temperature condition is very important when the screw machine is used for plasticizing. The practice shows that the barrel temperature should be 95~110 ℃, and the opening temperature should be 80~90 ℃. Because the barrel temperature is higher than 110 ℃, the plasticity of raw rubber will not change greatly. If the barrel temperature exceeds 120 ℃, the glue discharge temperature is too high to make the film sticky and stick to the roller, which is difficult to supplement processing. When the barrel temperature is lower than 90 ℃, the equipment load increases, and the plastic mixing rubber will be sandwiched.
It is more difficult to melt synthetic rubber than natural rubber. In order to improve the plasticizing process performance of synthetic rubber, it is better to control and adjust the molecular weight size and molecular weight distribution during the synthesis process, so as to produce varieties with low Mooney viscosity and good process performance, such as soft styrene butadiene rubber and soft nitrile rubber. These varieties can be directly used for mixing. Cis polybutadiene rubber has low molecular weight, is easy to cold flow, and has poor plasticizing effect. Therefore, cis polybutadiene rubber and appropriate Mooney viscosity should also be obtained from synthetic seeds. The chloroprene rubber Mooney viscosity is low, and generally does not need to be plasticized. It can be mixed after 3-5 passes. The Mooney viscosity of hard nitrile rubber is 90~120, with low plasticity and poor process performance. It can only be further processed after full plasticization. However, due to the high toughness of nitrile rubber, large heat generation and severe shrinkage during plasticizing, plasticizing is particularly difficult. To improve the plasticizing effect of nitrile rubber, the low temperature thin pass method should be adopted, that is, the plasticizing temperature should be reduced as much as possible and the mechanical force should be strengthened. Although the plasticizing effect of nitrile rubber can be improved by adding plasticizer. However, it is unfavorable to the improvement of the plasticity of the rubber mixture, so it should not be used. The chemical properties of butyl rubber and ethylene propylene rubber are stable, so they lack the plasticizing effect. The Mooney viscosity of the former is generally 38~75, which can be directly mixed without plasticizing. The plasticity necessary for the processing of the latter should be obtained during the synthesis process.