Mold costs depe…
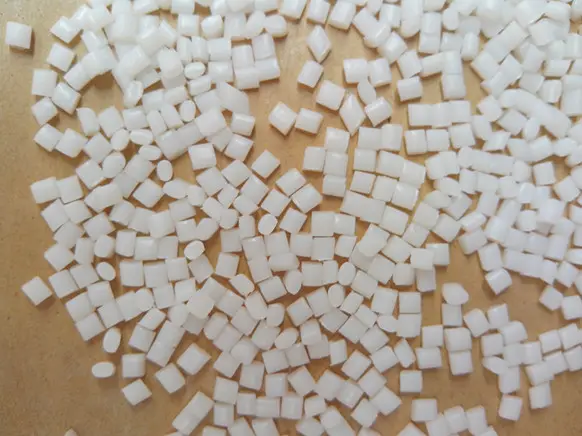
Injection Molding Data – 20 Plastic Properties(down)
PA12 polyamide 12 or nylon 12 typical application range: water meter and other commercial equipment, cable sleeve, mechanical cam, sliding mechanism and bearing, etc.
Process conditions of injection mold: drying treatment: humidity shall be below 0.1% before processing. If the material is stored in the air, it is recommended to dry it in 85C hot air for 4-5 hours. If the material is stored in a closed container, it can be directly used after 3 hours of temperature balance.
Melting temperature: 240~300C; Do not exceed 310C for materials with ordinary characteristics, and do not exceed 270C for materials with flame retardant characteristics.
Mold temperature: 30~40C for unreinforced materials, 80~90C for thin-walled or large-area components, and 90~100C for reinforced materials. Increasing the temperature will increase the crystallinity of the material. It is important for PA12 to accurately control the mold temperature. Injection pressure: up to 1000bar (low holding pressure and high melting temperature are recommended). Injection speed: high speed (better for materials with glass additives).
Runner and gate: For materials without additives, the runner diameter should be about 3mm due to the low viscosity of the material. For reinforced materials, 5~8mm large runner diameter is required. The runner shape should be all round. The injection port shall be as short as possible. Multiple forms of gates can be used. Do not use small gate for large plastic parts, which is to avoid excessive pressure on plastic parts or excessive shrinkage. The gate thickness should be equal to the thickness of the plastic part. If submerged gates are used, a minimum diameter of 0.8 mm is recommended. Hot runner molds are effective, but require precise temperature control to prevent material leakage or solidification at the nozzle. If a hot runner is used, the gate size should be smaller than the cold runner.
Chemical and physical properties: PA12 is a linear, semi crystalline crystalline thermoplastic material from butadiene. Its characteristics are similar to PA11, but its crystal structure is different. PA12 is a good electrical insulator and like other polyamides, it will not affect the insulation performance due to moisture. It has good impact resistance and mechanical and chemical stability. PA12 has many improved varieties in plasticizing and strengthening properties. Compared with PA6 and PA66, these materials have lower melting point and density, and have very high moisture regain. PA12 has no resistance to strong oxidizing acids. The viscosity of PA12 mainly depends on humidity, temperature and storage time. It has good liquidity. Shrinkage is between 0.5% and 2%, which mainly depends on material type, wall thickness and other process conditions.
Typical application scope of PS polystyrene: product packaging household utensils, trays, electrical (transparent containers, light scattering devices, insulating films, etc.).
Injection mold process conditions: drying treatment: drying treatment is usually not required unless improper storage. If drying is required, it is recommended that the drying condition be 80C for 2-3 hours. Melting temperature: 180~280C. For flame retardant materials, the upper limit is 250C. Mold temperature: 40~50C. Injection pressure: 200~600bar. Injection speed: fast injection speed is recommended. Runners and Gates: All generic types of gates can be used.
Chemical and physical properties: Most commercial PS are transparent, amorphous materials. PS has very good geometric stability, thermal stability, optical transmission characteristics, electrical insulation characteristics and very small moisture absorption tendency. It can resist water and diluted inorganic acid, but can be corroded by strong oxidizing acid such as concentrated sulfuric acid, and can expand and deform in some organic solvents. The typical shrinkage is 0.4~0.7%.
Typical application range of PVC: water supply pipeline, household pipeline, house wallboard, commercial machine shell, electronic product packaging, medical equipment, food packaging, etc.
Injection mold process conditions: drying treatment: drying treatment is usually not required. Melting temperature: 185~205C Mold temperature: 20~50C Injection pressure: up to 1500bar Holding pressure: up to 1000bar Injection speed: to avoid material degradation, the injection speed is generally equivalent. Runners and Gates: All regular gates can be used. If machining smaller parts, it is better to use a pin type gate or a submerged gate; For thicker assemblies, it is best to use a sector gate. The minimum diameter of pin type gate or submerged gate shall be 1mm; The thickness of sector and gate shall not be less than 1mm.
Chemical and physical properties: Rigid PVC is one of the most widely used plastic materials. PVC material is a kind of non crystalline material. In actual use, PVC materials are often added with stabilizers, lubricants, auxiliary processing agents, pigments, impact agents and other additives. PVC material has non flammability, high strength, weather resistance and excellent geometric stability. PVC has strong resistance to oxidants, reducing agents and strong acids. However, it can be corroded by concentrated oxidizing acids, such as concentrated sulfuric acid and concentrated nitric acid, and is not suitable for contacting aromatic hydrocarbons and chlorinated hydrocarbons. The melting temperature of PVC during processing is a very important process parameter. If this parameter is improper, it will lead to the problem of material decomposition. The flow characteristics of PVC are quite poor, and its process range is very narrow. In particular, PVC materials with large molecular weight are more difficult to process (such materials usually need to add lubricant to improve flow characteristics), so PVC materials with small molecular weight are usually used. The shrinkage of PVC is quite low, generally 0.2~0.6%.
Typical application scope of SA styrene acrylonitrile copolymer: electrical sockets, shells, etc., kitchen appliances for daily commodities, refrigerator devices, TV bases, cassette boxes, etc., automobile industry (headlight box, reflector, dashboard, etc.), household products (tableware, food knives, etc.), cosmetic packaging, etc.
Injection mold process conditions: drying treatment: SA has some hygroscopic properties if not properly stored. The recommended drying condition is 80C for 2-4 hours. Melting temperature: 200~270C. If thick wall products are processed, the melting temperature below the lower limit can be used. Mold temperature: 40~80C. For reinforced materials, the mold temperature should not exceed 60C. The cooling system must be well designed, because the mold temperature will directly affect the appearance, shrinkage and bending of products. Injection pressure: 350~1300bar. Injection speed: High speed injection is recommended. Runners and Gates: All regular gates can be used. The gate size must be adequate to avoid streaks, burns and voids.
Chemical and physical properties: SA is a hard, transparent material. Styrene makes SA hard, transparent and easy to process; The acrylonitrile component makes SA chemically and thermally stable. SA has strong load bearing capacity, chemical reaction resistance, thermal deformation resistance and geometric stability. The addition of glass fiber additive in SA can increase the strength and thermal deformation resistance, and reduce the thermal expansion coefficient. Vicat softening temperature of SA is about 110C. The deflection temperature under load is about 100C. The shrinkage of SA is about 0.3~0.7%.
Allyl ester resin
Allyl esters are allyl based esters. Allyl esters based on monobasic or dibasic acids can be used as low viscosity monomers or thermoplastic prepolymers. They are often used as cross-linking agents for unsaturated resins, as well as in the processing and molding of reinforced thermosetting molding materials and high-performance transparent materials.
Under high temperature and high humidity conditions, the resin still maintains its original electrical properties, and the molded products have the advantages of dimensional stability, chemical resistance, good mechanical strength and good heat resistance. Allyl ester resin molding compounds with flame retardants can be purchased in the market, and some varieties have been approved by Underwriters Laboratories of the United States. Some resins, tested with very thin test pieces, have a fire resistance grade of UL94 V-0 flammability grade, and are resistant to strong arc ignition and arc tracking.
Chemistry and Properties
The most widely used commercial allyl esters are diallyl phthalate and diallyl isophthalate monomers and prepolymers, which are easily converted into thermosetting molding compounds and prepregs of glass cloth and paper.
Diethylene glycol bis (allyl carbonate)
Because of its excellent transparency, it is used more and more widely. Because of its portability, stable size, wear resistance and easy colouring, it is the main material for making plastic lenses. Other applications include dashboard covers, camera filters, and areas of the rapidly growing glass industry.
Recently, a modified bisphenol A bis (allyl carbonate) has emerged. It is a transparent polymer with a high refractive index (1.56), which is higher than that of diethylene glycol bis (allyl carbonate). In addition, there is also a modified type used in lens design, which can change the lens design. Other commercial monomers are diallyl fumarate and diallyl maleate. This is a kind of trifunctional monomer with high reactivity, which contains two kinds of double bonds for polymerization. Allyl methacrylate also has bifunctional properties and can be used as crosslinking agent and monomer intermediate. Diallyl cyanurate can be used as crosslinking agent of unsaturated polyester resin.
Typical catalytic systems are peroxides, such as tert butyl perbenzoate, benzoic acid peroxide or dicumyl peroxide, which have sufficient thermal stability and can last until the crosslinking is completed. The best products are diethylene glycol bis (allyl carbonate) and diisopropyl peroxydicarbonate, because they are not only light in color, but also highly transparent. The amount of initiator is generally 2-3 parts per 100 parts of resin.
classification
The molding grade is mainly fiber filled, and the filled fibers include mineral fiber, glass fiber and synthetic fiber. This kind of molded products has excellent electrical properties and low loss factor under high temperature and high humidity conditions. High surface resistance and volume resistance, high arc resistance and arc track resistance. The insulation strength of diallyl phthalate is still good at 374 ° F, while diallyl isophthalate is still good when it can exceed 400 ° F.
application
Most diallyl phthalate compounds are commonly used in key parts of electrical or electronic equipment to ensure highly reliable performance under harsh environmental conditions.
A very important application field is the electrical connection devices used in communication, computer and aerospace systems. Other applications include insulators, potentiometers, circuit boards, switches, television components, etc. These polymer materials have a high degree of compatibility with modern electronic finishing technologies, such as vapor phase consolidation technology.
Reinforced plastics. Allyl ester resin is preimpregnated on glass cloth or roving to make tubes, conduits, radomes, junction boxes, aircraft and missile parts, etc.
Allyl ester monomer for polyester. Some allyl ester monomers are widely used as cross-linking agents for preformed polyester or felt adhesives, as well as for laminated prepreg or wet paving materials, as well as for pure materials, granules and premixed molding plastics, and for the processing and molding of glass cloth and decorative laminates. Due to the low steam pressure at the molding temperature, it is 2.4 mmHg at 302 ° F. Therefore, diallyl phthalate or other low volatile allyl ester monomers are commonly used in the manufacture of finished products, especially in the manufacture of large finished products, and styrene is rarely used.
Due to its low volatility, allyl polyester can be molded at a higher temperature than styrene polyester, so the molding cycle is faster.