Mold costs depe…
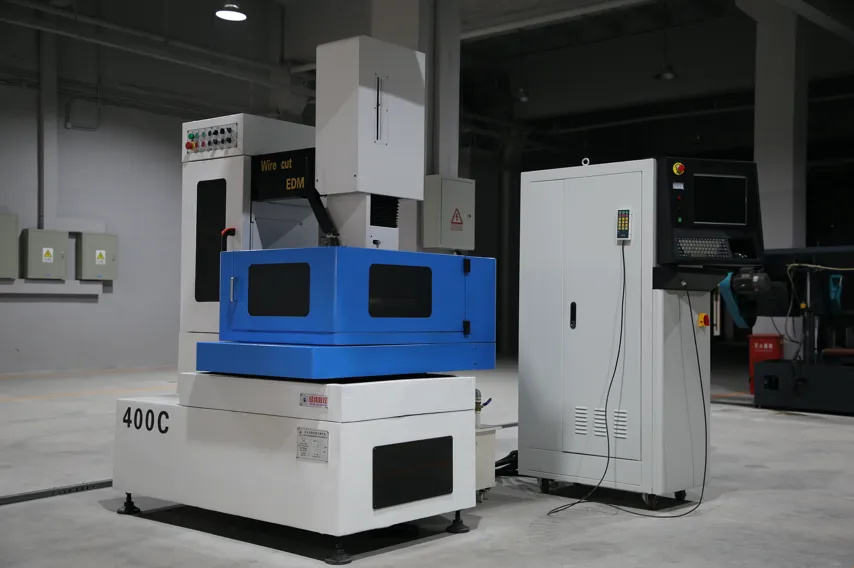
How can machine tools meet the requirements of high-speed cutting
1. The mechanism is designed for high-speed operation
High speed machine tool requires its mechanism to be highly rigid, capable of absorbing high frequency vibration and high inertia G value to ensure high speed cutting precision and stability. The spindle speed has reached a high level, which requires that the high-speed spindle should have a good lubrication and cooling system and conform to the principle of short, light and thin.
As one of the executive mechanisms of high-speed machining, high-speed feed mechanism is required to meet the requirements of acceleration and deceleration of high-speed feed, and must achieve high accuracy. Therefore, the actual transmission of servo motor and ball screw without backlash and LOSSMOTION phenomenon can show the effect in high feed cutting; The design of the ball screw mechanism should also ensure the positioning accuracy and prevent thermal displacement errors; The Z-axis requires lightweight, because the Z-axis must be sensitive to up and down reactions without interference jitter, and a special electric control circuit design is required, so that the Z-axis will not fall down even in the case of instant power failure, causing damage to the tool insertion. The mold processing is generally a long time processing, so the high speed running heat of the spindle inverter for a long time increases, which is easy to cause the aging of electronic parts. Therefore, the electric control box needs to use a closed air conditioning system to ensure the life and stability of the parts in the box and prevent oil contamination from entering.
2. Excellent CNC control system
CNC numerical control system is the unit that sends the position command. The command is required to be transmitted accurately and quickly. After processing, it sends the position command to each coordinate axis. The servo system must quickly drive the tool or workbench to move accurately according to the command. It requires to be able to process program segments quickly and control the machining error to the minimum. In the field of high-speed processing applications, Siemens 840D and Fanuc18iMB are the most representative.
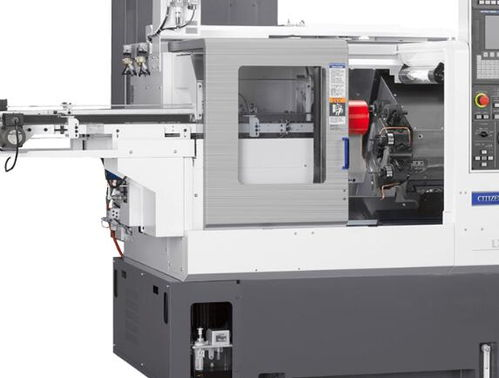
3. Tool handle and tool suitable for high-speed operation
Tools for high-speed cutting, especially high-speed rotary tools, require better quality and performance of tools and tool handles in terms of ensuring machining accuracy and operating safety. For tools, it is better that the slenderness ratio is less than 10 times. There are tungsten carbide tools, CBN tools and titanium coated tungsten carbide tools. For the tool handle, its dynamic balance is required to be less than 2.5G, and HSK, BBT (BTF-B) and some special tool handles can well meet the above requirements.
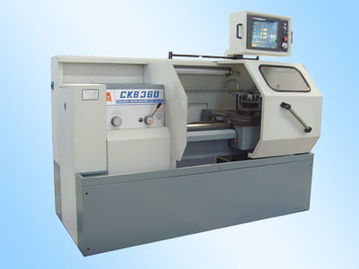
Professional CAD/CAM software requires a precise path calculation method, which can not only accurately meet the accuracy requirements of 3DProfile, but also reduce the discharge process, and even meet the surface quality requirements without polishing. It must be able to produce a good cutting path, make the cutting amount stable, not only improve the machining efficiency, but also extend the tool life and save the tool cost. Due to the diversity of design software, it needs to have good file transfer compatibility with other software, which can easily accept the drawings and files transferred by other software without distortion. Even if there are small holes or segment differences, they can be quickly repaired in the built-in 2D and 3DCAD, so as to hold the loopholes for users and grasp the timeliness.