Mold costs depe…
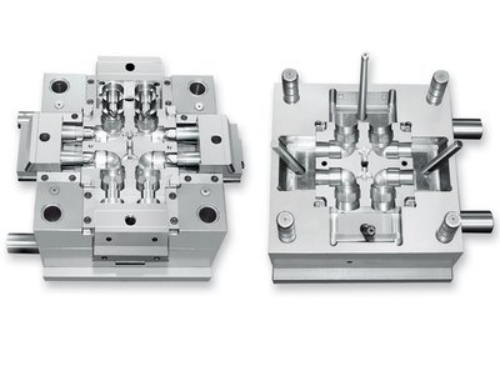
Why is mould known as “the mother of industry”
Moulds are various molds and tools used in industrial production to obtain required products by injection molding, blow molding, extrusion, die-casting or forging molding, smelting, stamping and other methods.
In short, a mold is a tool used to make molded articles. This tool is composed of various parts. Different molds are composed of different parts. It mainly realizes the processing of article shape by changing the physical state of the formed materials.
Mold composition
The die has a specific contour or cavity shape, and the contour shape with the cutting edge can make the blank separate according to the contour shape, that is, blanking; The inner cavity shape can make the blank obtain corresponding solid shape.
The die is generally divided into two parts: movable die and fixed die, or male die and female die, which can be separated and combined. When separating, the blank is put in or taken out, and when closing, the blank is separated from the blank or formed.
In the process of blanking, forming stamping, die forging, cold heading, pressing and compression molding, the external force required for separation or forming is exerted on the blank through the die; In the process of extrusion, die casting and injection molding, the external force is exerted on the blank by air pressure, plunger, punch, etc. The die bears the expansion force of the blank.
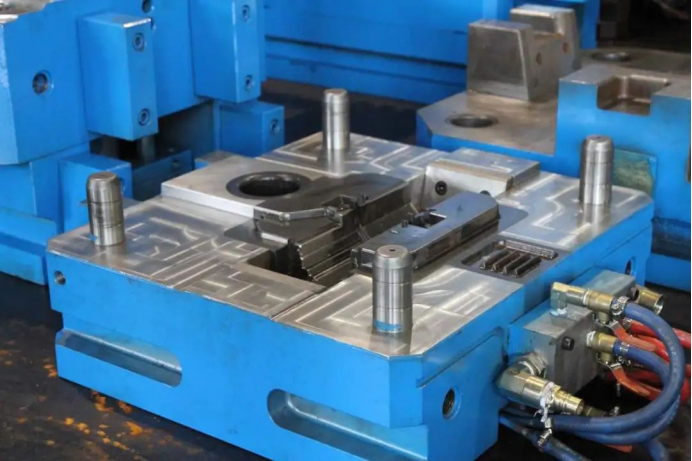
In addition to the mold itself, the mold base, mold base, guide device, and parts output device are also required. These parts are generally made into universal type to apply to a certain range of different molds.
The mold is basically produced by single piece, and its shape is complex. It has high requirements for structural strength, stiffness, surface hardness, surface roughness and machining accuracy, so the mold production needs a high level of technology.
The timely supply and quality of moulds directly affect the quality, cost and development of new products. Therefore, the level of mold production is one of the important signs of the level of mechanical manufacturing
Classification of moulds
According to the different materials formed, the mold can be divided into metal mold and non-metal mold. Metal mold is divided into: die-casting mold, extrusion mold, stamping mold and so on; Non metal molds are also divided into plastic molds and inorganic non-metallic molds.
Subdivided molds include: die, plastic mold, die-casting mold, forging mold, powder metallurgy mold, drawing mold, extrusion mold, rolling mold, glass mold, rubber mold, ceramic mold, etc
Stamping die
The mold that separates, forms or joins metal, non-metallic sheet or profile into products or parts under pressure. Including: blanking die, drawing die, bending die, progressive die, fine blanking die, finishing die, etc
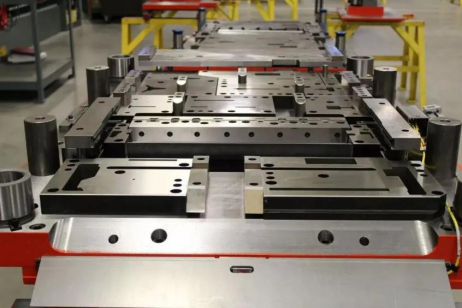
Plastic mould
The molten plastic raw materials are filled into the mold cavity under the action of pressure, and solidified into a mold for products and parts. Including injection mold, compression mold, pressure injection mold, extrusion mold, blow molding mold, thermoforming mold, foaming mold, etc
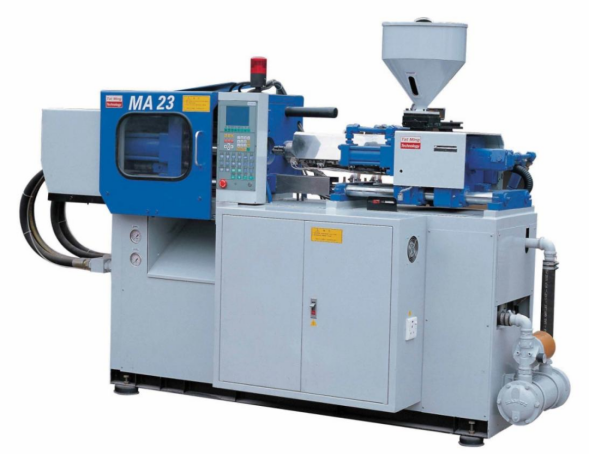
Die-casting die
The mold that makes the liquid metal fill the mold cavity rapidly under the action of pressure and cool and solidify to form parts
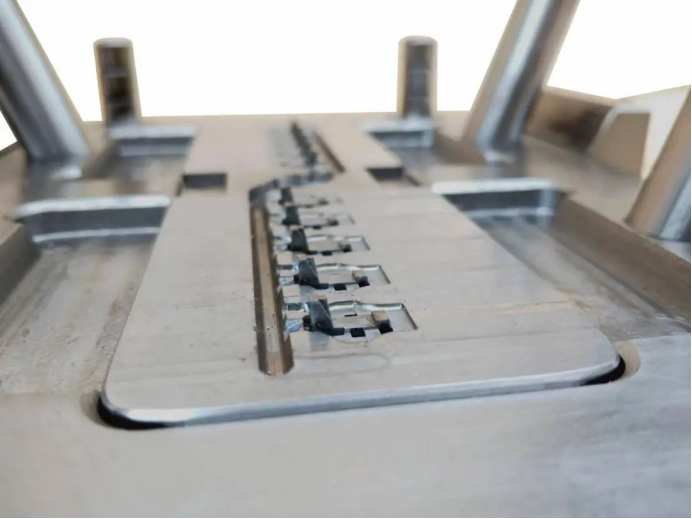
forging die
A die for forming metal blanks into blanks and workpieces under pressure. Including: hammer forging die, mechanical press forging die, screw press forging die, hydraulic press forging die, flat forging die, etc
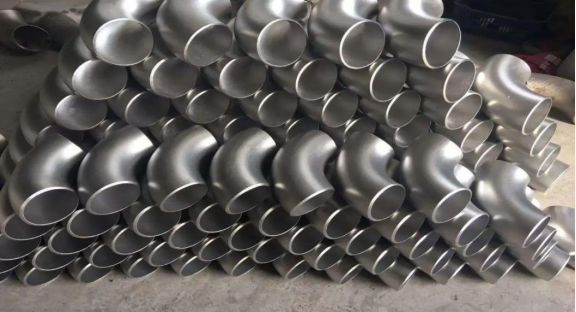
Powder metallurgy mold
A mold for forming metal and nonmetal powders into blanks or products by powder metallurgy process. Including: pressing die, isostatic pressure die, injection die, extrusion die, shaping die, etc
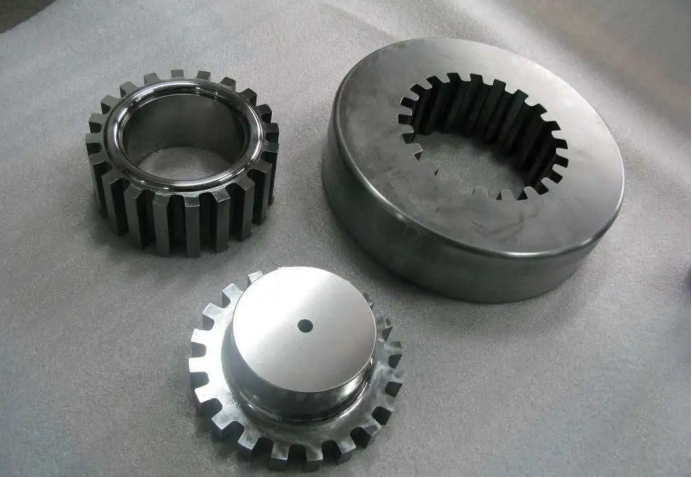
Drawing die
It is a die that can make the metal blank stretch and deform into bars, wires, wires, profiles, parts and other products and parts through the cross hole under the tensile force. Including: steel drawing die, carbide drawing die, diamond drawing die, diamond coating drawing die, ceramic drawing die, etc
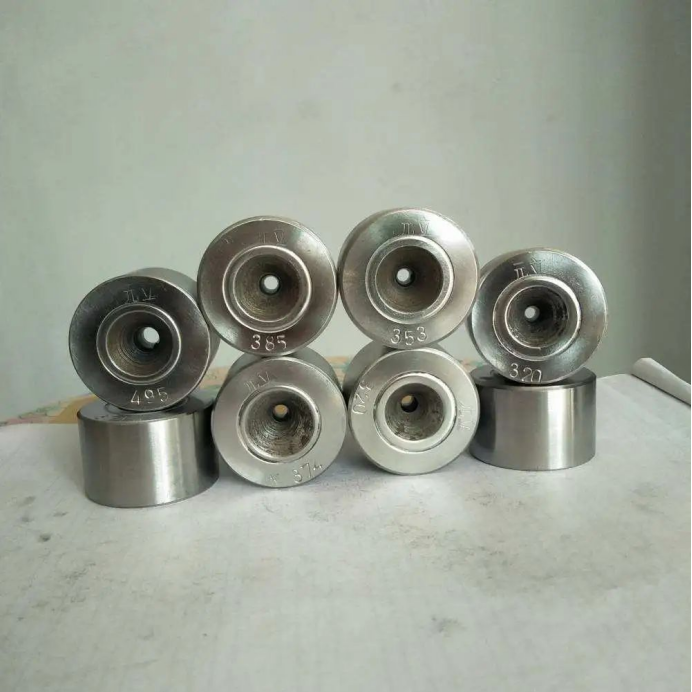
Extrusion die
A die that causes the metal blank to produce plastic deformation under the action of extrusion force to form profiles or products or parts. Including: reverse extrusion die, forward extrusion die, forward and reverse extrusion die, radial extrusion die, upsetting extrusion compound die, etc
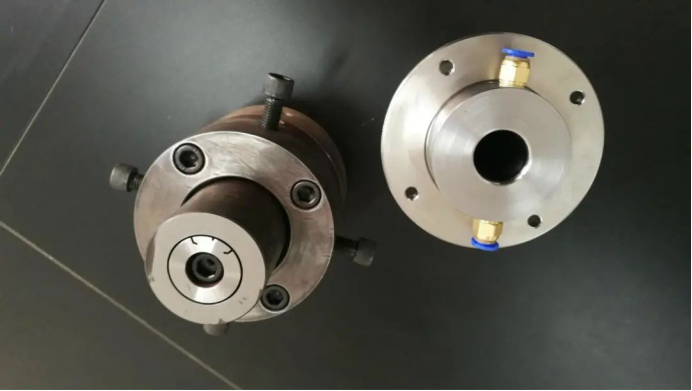
Rolling die
The roll mould that separates, forms, compounds, corrects, joins or transfers metal or nonmetal plates, profiles and bars into products and parts under rotary pressure. Including: roll die, roll bending die, etc.
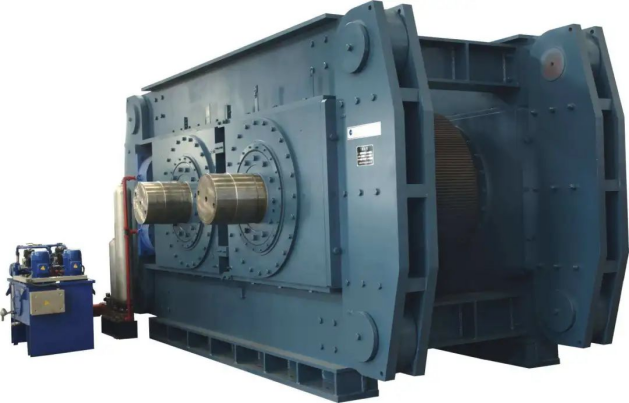
Glass mold
The glass raw material is molded into a mold for making mouth and parts. Including: bottle mold, vessel mold, hot forming mold, drawing mold, pressing mold, blowing mold, centrifugal mold, pressing mold, etc
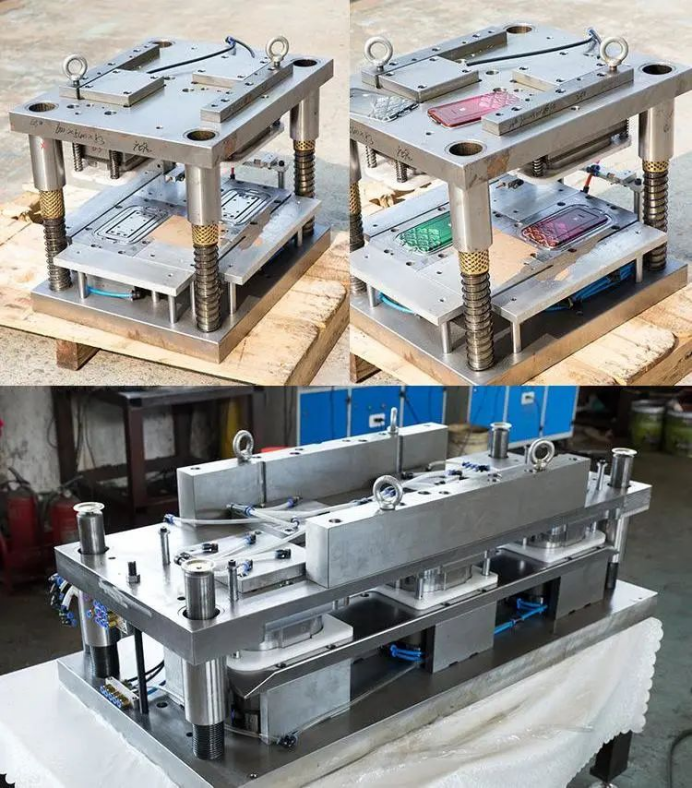
Rubber mold
Make rubber raw materials into molds for products and parts. Including: vulcanized rubber mold, thermoplastic rubber mold, liquid rubber mold, latex mold, compression mold, injection mold, extrusion mold, tire mold, tire molding drum mold, etc
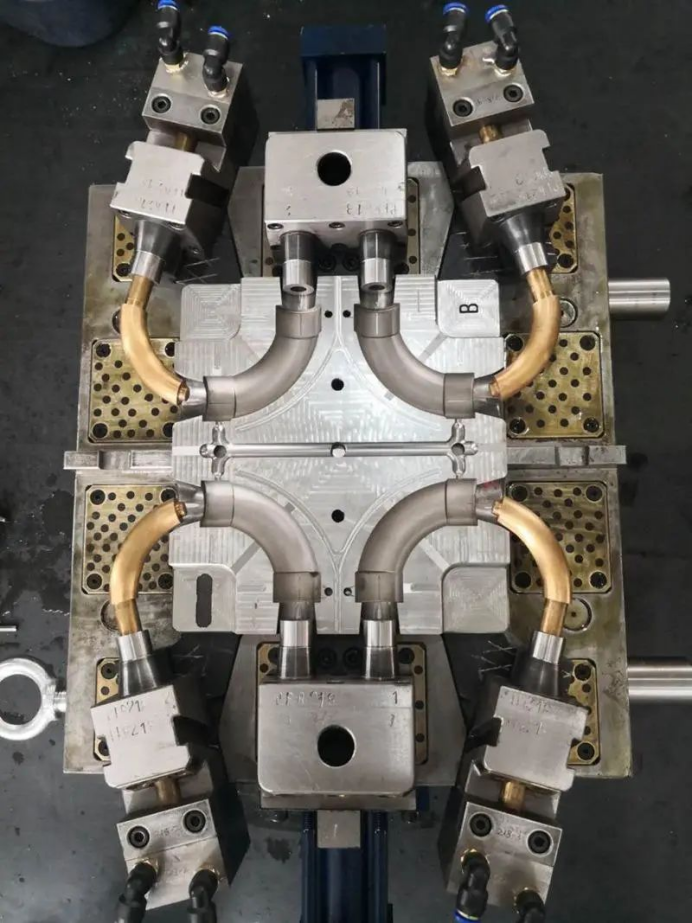
Ceramic mold
A mold for forming ceramic raw materials into blanks and products. Including: plastic forming die, rolling forming die, extrusion forming die, grouting forming die, pressing forming die, isostatic pressure forming die, etc
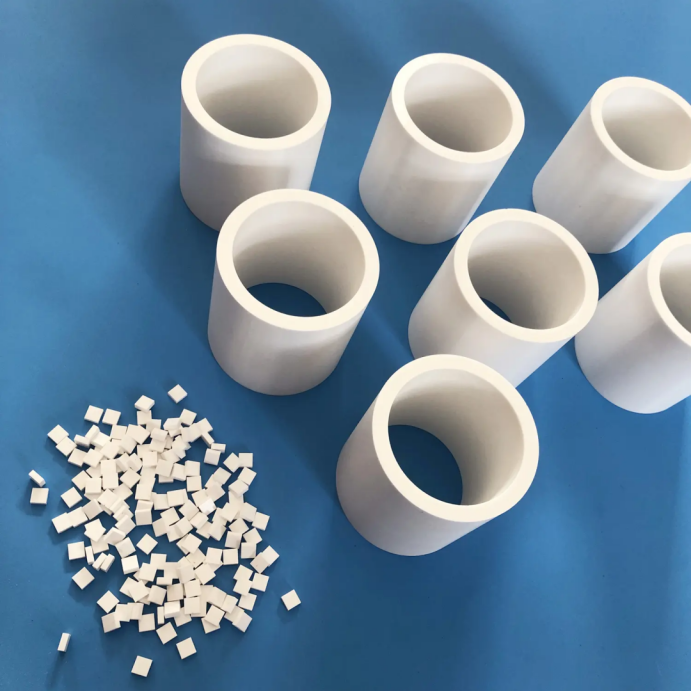