Mold costs depe…
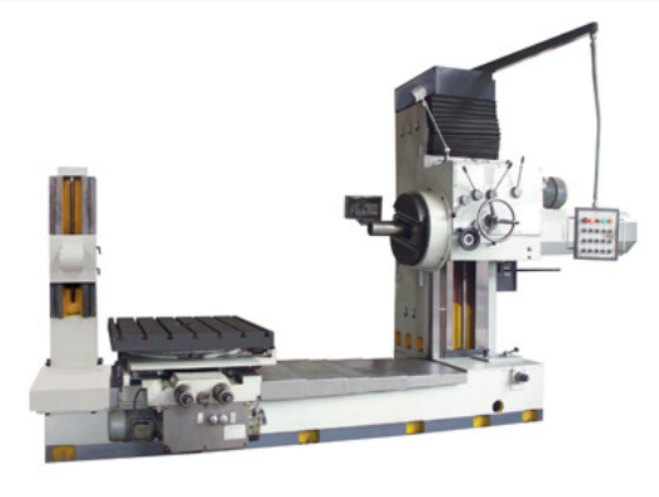
Common machine tools for machining and their application scope
With the increase of market demand for machining, the technical accuracy of machining is also improved, and the types of machine tools are more and more.
According to the classification of processing methods and tools used, machine tools are classified into 11 categories: lathe, drilling machine, boring machine, grinder, gear processing machine, thread processing machine, milling machine, planer, puller, sawing machine, etc.
There are seven categories of commonly used boring machines, grinders, lathes, planers, milling machines, drilling machines, and gear processing machines
Boring machine
The boring machine is suitable for plane milling and hole series processing of single or small batch production parts in the machining workshop. The spindle box end is designed with a flat rotary table radial tool holder, which can accurately bore holes and planes with large size.
Boring machine is also divided into CNC boring machine and CNC coordinate boring machine, both of which are vertical and horizontal. The control mode of the boring machine is point position and straight line, which is used to process box parts and requires manual tool change; The control mode of the coordinate boring machine is point position and straight line, which is used to process box parts with high hole spacing requirements, and also requires manual tool change
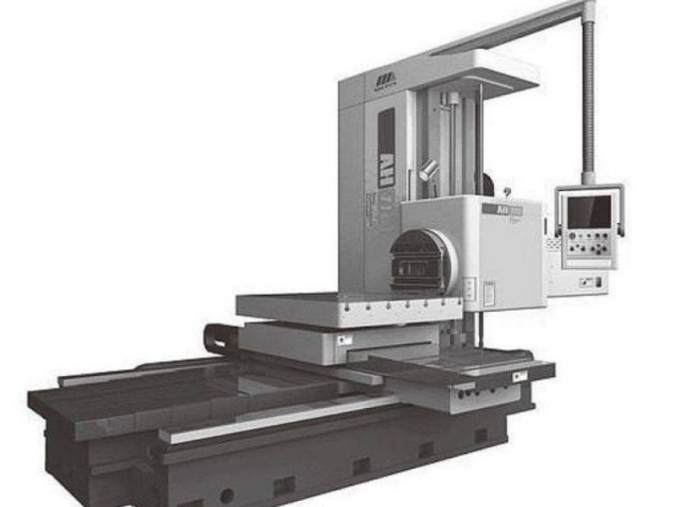
Grinding machine
The machine tool that uses abrasive abrasive tools (grinding wheel, abrasive belt, oilstone or abrasive material, etc.) as tools to cut the workpiece surface is collectively referred to as the grinder.
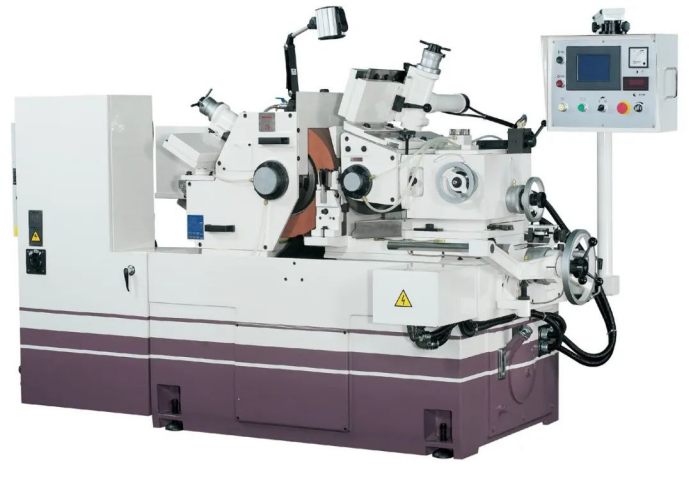
It is mainly used for rough and fine plane grinding, mirror grinding, shaping grinding after grinding wheel modification; Automatic correction of grinding wheel, etc; Centerless grinding machine does not need pre turning for direct grinding, and centerless form grinding; Special grinders include lead screw grinder, spline grinder, curved wheel grinder, camshaft grinder, etc.
Because it is easy to obtain high machining accuracy and good surface quality during grinding, the grinder is mainly used for finishing parts, especially hardened steel parts and high hardness special materials
Lathe
The lathe is mainly used to process various rotary surfaces and end faces of rotary bodies. The equipment can be horizontal or vertical.
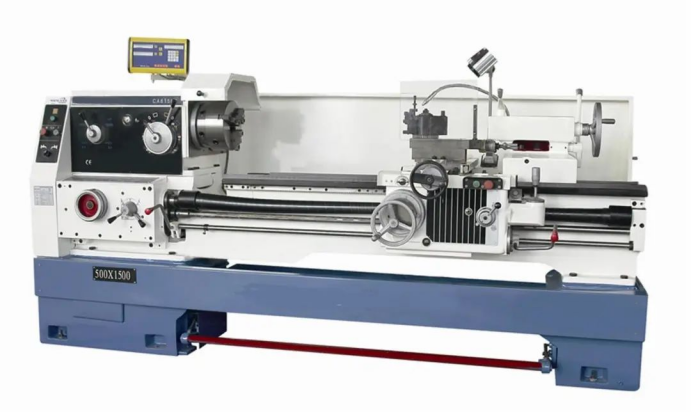
The control mode of chuck horizontal lathe is point position and straight line, which is used to process small disk parts. Square tool rest or turret is adopted; The control mode of the center horizontal lathe is contour, which is used to process disk and shaft parts. The lathe bed can be horizontal, vertical or inclined, and the square tool rest or rotary tool magazine is used.
The control mode of vertical CNC lathe is contour, which is used to process large continuous control panel parts and adopts turret tool rest
facing machine
The planer is mainly used to process various planes (such as horizontal plane, vertical plane, inclined plane and various grooves, such as T-shaped groove, dovetail groove, V-shaped groove, etc.) and linear formed surfaces.
If equipped with profiling device, it can also process spatial curved surface, such as turbine impeller, spiral groove, etc. This type of machine tool has a simple tool structure and does not cut during the return trip, so its productivity is low. It is generally used for single piece small batch production
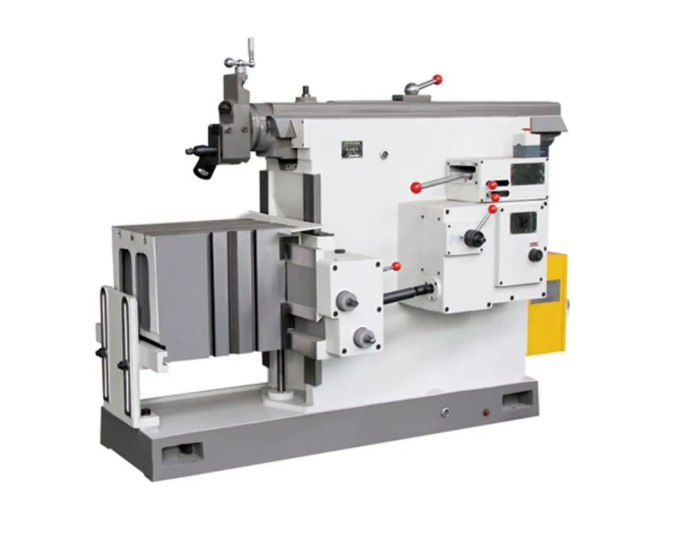
Milling Machine
A machine tool with a wide range of uses, which can process plane (horizontal plane, vertical plane), groove (keyway, T-shaped groove, dovetail groove, etc.), tooth splitting parts (gear, spline shaft, sprocket, spiral surface (thread, spiral groove) and various curved surfaces on the milling machine. It can also be used to process the surface and inner hole of the rotary body and cut off.
When the milling machine is working, the workpiece is installed on the workbench or indexing head and other accessories. The milling cutter rotates mainly, supplemented by the feed movement of the workbench or milling head, and the workpiece can obtain the required machining surface. The productivity of the milling machine is high because it is multi cutter intermittent cutting.
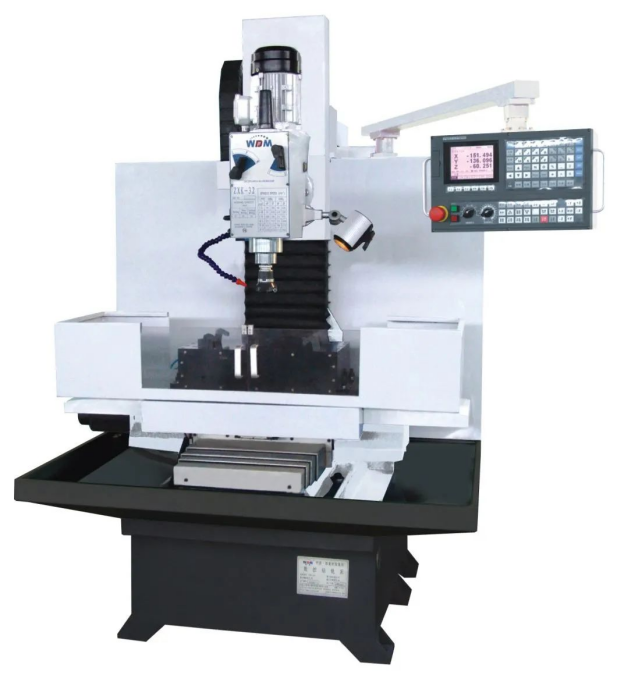
Milling machines can be divided into vertical type and gantry type. The control mode of vertical CNC milling machine includes point position, straight line, contour (multi axis linkage), milling, form milling (also can drill holes and tap threads), and manual tool change.
The control mode of gantry CNC milling machine is point position, straight line and contour (multi axis linkage), which is used to process large and complex parts and manually change tools.
In addition, there is also a CNC profiling milling machine on the market, which can be divided into vertical and horizontal types. The control mode is contour (multi axis linkage), which is used to process concave and convex dies and manually change tools
Drilling Machine
A drilling machine is a general-purpose machine tool with a wide range of uses, which can drill, counterbore, ream, countersink and tap threads on parts. When the radial drilling machine is equipped with process equipment, it can also be used for boring; The universal workbench is equipped on the bench drill, and the keyway can also be milled
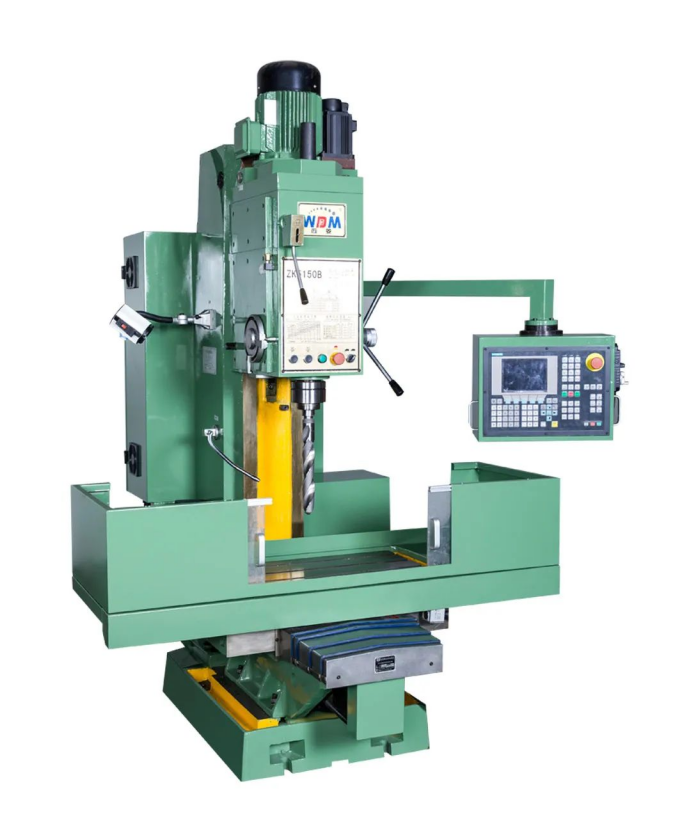
The drilling machine is divided into single and double workbenches, and the control mode is point position, straight line, which can drill, ream and tap threads; Two fixed workbenches, one for machining, the other for loading and unloading parts, linear tool magazine
Gear processing machine
Gear Cutting Machine
The gear processing machine tool is used to process the teeth of various cylindrical gears, bevel gears and other parts with teeth. The control mode is linear, and the tooth profile generates movement. According to different processing methods, it can be divided into gear hobbing machine, gear shaping machine and gear grinding machine.
hobbing machine:
On the gear machine, straight and helical cylindrical gears can be cut, and worm gears, sprockets, etc. can also be machined. It is a gear processing machine tool that uses a hob to process spur, helical, herringbone cylindrical gears and worm gears according to the generating processing method. This machine tool can also process various special tooth shaped workpieces such as splines and sprockets when special hobs are used
The machining accuracy of ordinary gear hobbing machine is 7~6 grades (JB179-83), and that of high-precision gear machine is 4~3 grades, with the maximum machining diameter of 15m.
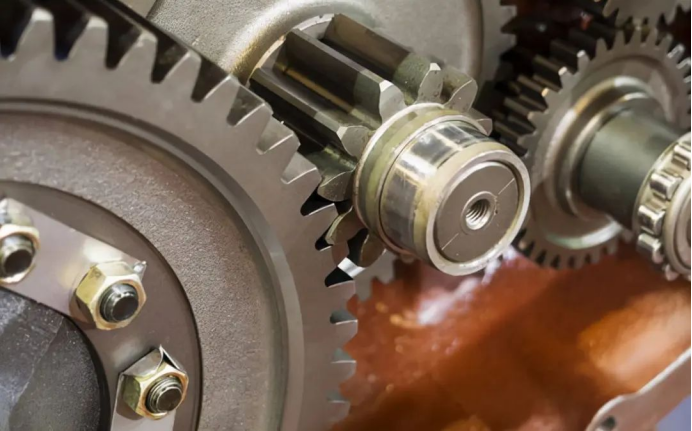
Gear shaper:
It is a gear processing machine tool that uses a gear shaper cutter to process internal and external straight and helical cylindrical gears and other gear shaped parts according to the generating method. During gear shaping, the gear shaper cutter performs up and down reciprocating cutting movement, while rolling relative to the workpiece.
The gear shaper is mainly used to process multiple gears and internal gears. It can also process racks after adding accessories. Using special tools on the gear shaper can also process non-circular gears, incomplete gears and internal and external formed surfaces, such as square holes, hexagonal holes, keyed shafts, etc. The machining accuracy can reach level 7~5 (JB179-83), and the maximum workpiece diameter can reach 12m.
Gear grinding machine:
Use the grinding wheel as the abrasive tool to process cylindrical gears or some gears (helical gears, bevel gears, etc.) to process the gears on the cutter tooth surface.
There are many kinds and specifications of gear processing machine tools, including small machine tools for machining gears with a diameter of several millimeters, large machine tools for machining gears with a diameter of more than ten meters, efficient machine tools for mass production and high-precision machine tools for machining precision gears.
Gear processing machine tools are widely used in various machinery manufacturing industries such as automobiles, tractors, machine tools, engineering machinery, mining machinery, metallurgical machinery, petroleum, instruments, aircraft and spacecraft