Mold costs depe…
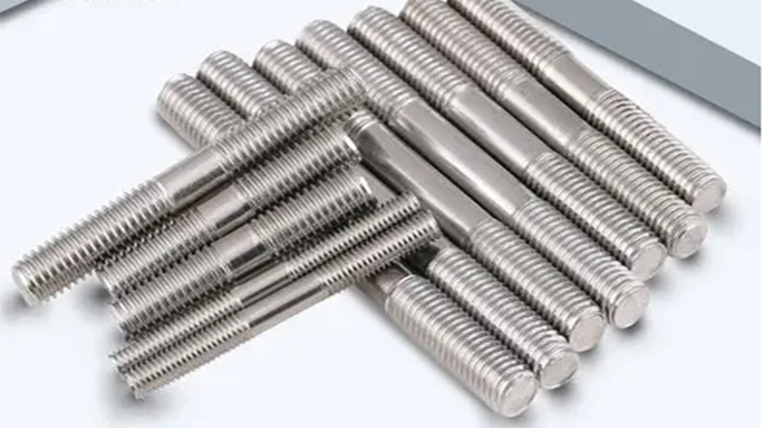
Machining method of common double thread
Screw threads are classified according to the number of spiral grooves on the thread in addition to the section shape. The thread with one spiral groove is called single head thread. Threads with more than two spiral grooves are called multi head threads. The distance between two adjacent spiral grooves on the thread is called pitch. The distance along the spiral groove is called lead.
The relationship between lead and pitch can be expressed by the following formula
L = t × Where, L – thread lead (mm),
N – Number of thread heads,
T – thread pitch (mm).
When turning multi head threads, the lead (mm) should be used on the tool feed box to adjust the position of the handle according to the provisions on the nameplate.
When turning multi head threads, there are two ways to solve the problem. The lead splitting method is called lead splitting method, and the other way is to split on the circumference of the thread, called circumference splitting method.
(1) Two methods are introduced separately on the lead of thread.
Use the scale of the dial on the small tool holder to divide the heads; Namely, the small tool holder scale is used to grasp the turning tool travel distance (the double head thread moves one pitch, that is, half lead), so as to achieve correct indexing. After turning a spiral groove, as long as the small tool holder is moved by a pitch distance according to the scale, another adjacent spiral groove can be turned. Use the dial indicator to determine the movement value of the small tool holder to divide the heads; That is, fix the dial indicator base on the bed saddle, and the measuring head of the dial indicator measuring rod is at the end of the slide plate of the small tool holder. The moving size of the small tool holder can be determined according to the reading on the dial indicator for dividing.
(2) The method of dividing the head on the circumference of the thread.
When the speed of the shaft on (Z1) and the spindle of the lathe is the same, and the number of teeth of the driving gear (Z1) is a multiple of the number of thread heads of the work-piece, after turning one end of the thread, mark 1 (Z1), 2 (Z2) on the position where the driving gear (Z1) and intermediate gear (Z2) mesh, and then disconnect the driving gear (Z1) and intermediate gear (Z2), Turn the driving gear (Z1) over a certain number of teeth (double thread to Z1/2, three thread to Z1/3), and then make it mesh with the intermediate gear (Z2) again, and then start turning the threads of other heads.
When the number of teeth of the driving gear (Z1) is not a multiple of the number of thread heads of the workpiece, after turning one end of the thread, mark 3 (Z3), 4 (Z4) on the engagement position of the lead screw gear (Z4) and intermediate gear (Z3), then disengage (Z4) and (Z3), and turn the lead screw gear (Z4) over a certain number of teeth [the number of teeth that the lead screw gear should turn (Z4)=the number of teeth of the driving gear (Z1) × Number of intermediate gear teeth (Z3)/number of thread heads × Number of teeth of intermediate gear (Z2)], and then make it mesh with intermediate gear (Z3) again, and then start turning other threads.