Mold costs depe…
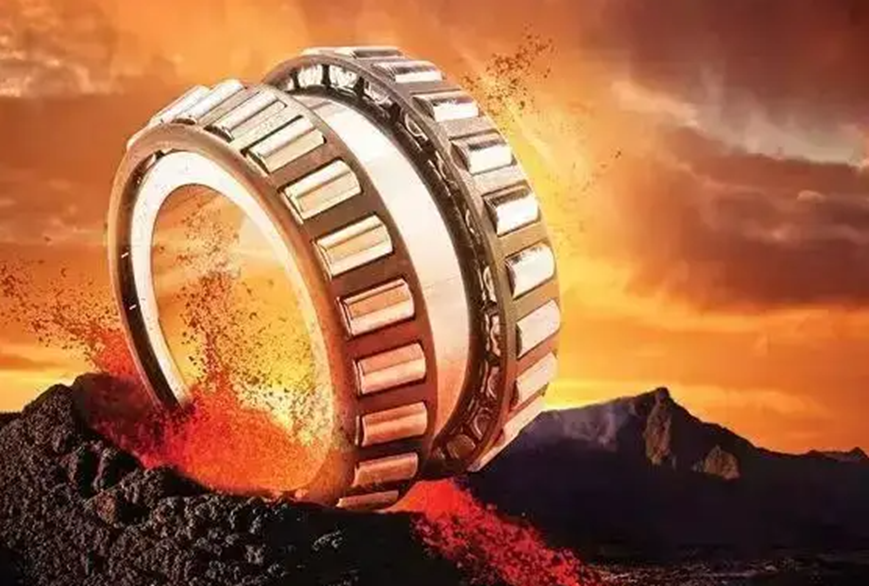
There are 12 heat treatment processes. After five minutes, you will have a qualitative change
1. Annealing
Operation method: After the steel is heated to the temperature of Ac3+30~50 ℃ or Ac1+30~50 ℃ or below (relevant materials can be consulted), it is usually cooled slowly with the furnace temperature.
Intention: 1. Reduce hardness, improve plasticity, and improve cutting and pressure processing functions; 2. Refine grains, improve mechanical functions, and prepare for the next process; 3. Eliminate the internal stress caused by cold and hot working.
Application keys: 1. It is applicable to forgings and weldments of alloy layout steel, carbon east and west steel, alloy east and west steel, high-speed steel, and raw materials with unqualified supply conditions; 2. Annealing is usually carried out in the blank condition.
2. Normalizing
Operation method: heat the steel to 30~50 degrees above Ac3 or Accm, and cool it at a cooling rate slightly higher than that of annealing after heat preservation.
Intention: 1. Reduce hardness, improve plasticity, and improve cutting and pressure processing functions; 2. Refine grains, improve mechanical functions, and prepare for the next process; 3. Eliminate the internal stress caused by cold and hot working.
Key to application: normalizing is usually used as the pre heat treatment process of forgings, weldments and carburized parts. Low carbon and medium carbon layout steel and low alloy steel parts with low functional requirements can also be used as final heat treatment. As for medium and high alloy steels, air cooling can cause complete or partial quenching, so it cannot be used as the final heat treatment process.
3. Quenching
Operation method: heat the steel piece to the phase change temperature Ac3 or above, keep it warm for a period of time, and then cool it rapidly in water, nitrate, oil, or air.
Purpose: Quenching is usually to obtain martensite arrangement with high hardness. Sometimes, when quenching some high alloy steels (such as stainless steel and wear-resistant steel), it is to obtain a single and uniform austenite arrangement to improve wear resistance and corrosion resistance.
Key application: 1. It is usually used for carbon steel and alloy steel with carbon content greater than 0.3%; 2. Quenching can give full play to the strength and wear resistance potential of steel, but it will form a large internal stress together, reducing the plasticity and impact toughness of steel, so tempering is required to obtain better inductive mechanical function.
4. Tempering
Operation method: Heat the quenched steel from the beginning to a temperature below Ac1, and cool it in air, oil, hot water and water after heat preservation.
Intention: 1. Reduce or eliminate the internal stress after quenching, and reduce the deformation and cracking of the workpiece; 2. Adjust the hardness, improve the plasticity and resistance, and obtain the mechanical functions required by the operation; 3. Dimension of stable workpiece.
Key points for application: 1. Insist on low temperature tempering for steel with high hardness and wear resistance after quenching; When improving the elasticity and yield strength of steel under the condition of adhering to a certain toughness, moderate tempering is used; High temperature tempering shall be used when high impact toughness and plasticity are adhered to and the strength is satisfied; 2. Generally, steel shall be prevented from tempering at 230~280 ℃ and stainless steel at 400~450 ℃ as far as possible, because once tempering brittleness will occur.
5. Quenching and tempering
Operation method: after quenching, high temperature tempering is called quenching and tempering. The steel shall be heated to a temperature 10~20 ℃ higher than that during quenching, quenched after heat preservation, and then tempered at a temperature of 400~720 ℃.
Intention: 1. Improve the cutting function and improve the surface finish; 2. Reduce deformation and cracking during quenching; 3. Achieve outstanding inductive mechanics function.
Application keys: 1. It is applicable to alloy layout steel, alloy east and west steel and high-speed steel with high hardenability; 2. It can not only be used as the final heat treatment of various important layouts, but also as the pre heat treatment of some tight parts, such as lead screws, to reduce deformation.
6. Aging
Operation method: heat the steel to 80~200 ℃, keep it warm for 5~20 hours or longer, and then take it out with the furnace and cool it in the air.
Intention: 1. The arrangement of the steel parts after quenching to reduce the deformation of the storage or use time; 2. Reduce the internal stress after quenching and grinding, and stabilize the shape and dimension.
Key application: 1. It is applicable to all kinds of steel after quenching; 2. It is commonly used for tight workpieces whose required shape no longer changes, such as tight lead screws, measuring objects, bed cases, etc.
7. Cold treatment
Operation method: cool the quenched steel parts in low temperature medium (such as dry ice and liquid nitrogen) to – 60~- 80 ℃ or lower, and take them out for uniform temperature to room temperature.
Intent: 1. Make all or most of the remaining austenite in the quenched steel parts convert to martensite, and then improve the hardness, strength, wear resistance and fatigue limit of the steel parts; 2. The arrangement of stabilizing steel shall be based on the shape and dimension of stabilizing steel parts.
Key points for application: 1. After quenching, steel parts shall be cold treated and then tempered at low temperature to eliminate the internal stress during low temperature cooling; 2. Cold treatment is mainly applicable to tight tools, measuring tools and tight parts made of alloy steel.
8. Flame heating surface quenching
Operation method: the flame burned with oxygen acetylene mixed gas is sprayed on the surface of the steel piece, heated rapidly, and cooled immediately when it reaches the quenching temperature.
Intention: to improve the external hardness, wear resistance and fatigue strength of steel parts, while maintaining the resistance in the heart.
Key points for application: 1. It is mainly used for medium carbon steel parts, and the depth of the hardened layer is usually 2~6mm; 2. It is applicable to large workpieces produced in single piece or small batch and workpieces requiring partial quenching.
9. Induction heating surface hardening
Operation method: put the steel piece into the inductor, make the steel piece surface produce induced current, heat it to the quenching temperature in a very short time, and then spray water for cooling.
Purpose: to improve the external hardness, wear resistance and fatigue strength of steel parts, and to adhere to the resistance of the heart.
Key application: 1. It is mainly used for medium carbon steel and alloy layout steel parts in the nave; 2. Because of the skin effect, the hardening layer of high-frequency induction hardening is generally 1~2mm, the medium frequency quenching is generally 3~5mm, and the high-frequency quenching is generally greater than 10mm.
10. Carburization
Operation method: put the steel piece into the carburizing medium, heat it to 900~950 degrees and keep it warm, so that the steel piece can obtain a carburized layer with a certain concentration and depth.
Purpose: to improve the external hardness, wear resistance and fatigue strength of steel parts, while the central part still adheres to the resistance.
Key points for application: 1. It is used for low carbon steel and low alloy steel parts with carbon content of 0.15%~0.25%, and the depth of carburized layer is usually 0.5~2.5mm; 2. After carburizing, it is necessary to conduct quenching to obtain martensite on the surface, and then carburizing can be completed.
11. Nitriding
Operation method: use the active nitrogen atom differentiated from ammonia at 5..~600 ℃ to saturate the steel surface with nitrogen to form a nitriding layer.
Purpose: to improve the hardness, wear resistance, fatigue strength and corrosion resistance of steel parts.
Key to application: It is mainly used for medium carbon alloy layout steel rich in aluminum, chromium, molybdenum and other alloy elements, as well as carbon steel and cast iron, with the nitriding layer depth of 0.025-0.8mm
12. Nitrocarburizing
Operation method: carburize and nitride the steel parts together.
Purpose: to improve the hardness, wear resistance, fatigue strength and corrosion resistance of steel parts.
Key points for application: 1. It is mainly used for low carbon steel, low alloy layout steel and east and west steel parts, and the nitriding layer is usually 0.02~3mm deep; 2. Quenching and low temperature tempering are required after nitriding.