Mold costs depe…
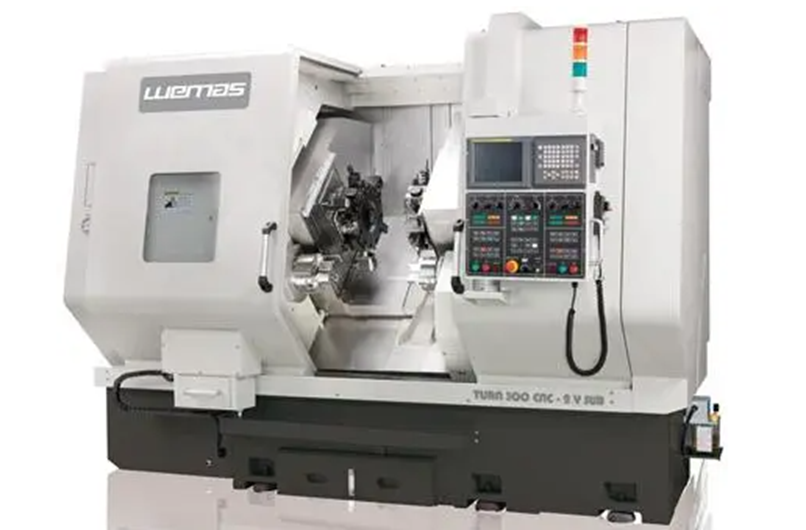
Lubrication Skills of Metal Cutting Machine Tools
Metal cutting machine tools (hereinafter referred to as machine tools) are a large number and a wide range of equipment. Their structural characteristics, machining accuracy, degree of automation, working conditions and operating environment conditions are very different, and they have different requirements for lubrication systems and lubricants used.
1、 Features and requirements of machine tool lubrication:
1. The main parts of machine tools are mostly typical mechanical parts, which are standardized, generalized and serialized. For example, the lubrication conditions of sliding bearings, rolling bearings, gears, worm gear pairs, rolling and sliding guides, screw drive pairs (screw nut pairs), clutches, hydraulic systems, cams, etc. are different.
2. Environmental conditions for the use of the machine tool: The machine tool is usually installed in an indoor environment. The maximum ambient temperature in summer is 40 ℃. In winter, when the temperature is lower than 0 ℃, the heating method is often used to make the ambient temperature higher than 5-10 ℃. High precision machine tools require a constant temperature and air conditioning environment, generally around 20 ℃. However, due to the high precision requirements and automation level of many machine tools, the requirements on viscosity, oxidation resistance (service life) and oil cleanliness are stricter.
3. Working conditions of machine tools: different types of machine tools with different specifications and sizes, even on the same machine tool, the working conditions are very different due to different machining parts. The requirements for lubrication vary. For example, the requirements for lubrication methods and lubricants of the grinding wheel spindle bearings of high-speed internal grinding machines are very different from those of the heavy-duty and low-speed spindle bearings of heavy-duty machine tools. The former needs to use oil mist or oil/air lubrication system for lubrication, and use lubricating oil with lower viscosity, while the latter needs to use oil bath or pressure circulating lubrication system for lubrication, and use oil with higher viscosity.
4. Adaptability of lubricating oil to lubricating coolant, rubber seals, paint materials, etc.: lubricating coolant is used on most machine tools. In lubricating oil, the oil is often emulsified and deteriorated due to the mixing of coolant, and the machine parts are rusted, which causes rubber seals to expand and deform, and the paint coating on the surface of parts to bubble and peel off. Therefore, consider the adaptability of oil products and lubricating coolant, rubber seals, paint materials, oil leakage prevention, etc. Especially with the improvement of machine tool automation, general lubricating/cooling oil is used on some automatic and CNC machine tools, which can be used as lubricating oil or lubricating coolant.
2、 Tips for using machine tool lubricant:
Due to the wide variety of metal cutting machine tools and the great changes in their structures and components, it is difficult to give a clear opinion on the selection of lubricants for their main components. The following contents are recommendations for the rational application of lubricants for some main components of machine tools according to relevant standards for reference.
1. Recommended lubricants for machine tools:
Total loss system: refined mineral oil, L-AN32, L-AN68 or L-AN220, used for light load components, often using HL hydraulic oil.
2. Gear (closed gear): continuous lubrication (splash, circulation or injection), refined mineral oil, and improved its oxygen resistance, corrosion resistance (ferrous and nonferrous metals) and foam resistance. CKB32, CKB68 or CKB100, CKB150. For closed gears with light load and small operation (related to main axle box bearing, tool box, sliding frame, etc.), CKB32 and CKB68 can also be used for overflow lubrication of mechanical control clutch, and CKB68 can replace AN68. HL type hydraulic oil is commonly used for machine tool spindle box; Refine mineral oil, and improve its oxygen resistance, corrosion resistance (black and non-ferrous metals), bubble resistance, extreme pressure and wear resistance. CKC100, CKC150, CKC200, CKC320, CKC460, any type of closed gear (except hypoid gear) and related bearings operating at normal or medium constant temperature and under heavy load, can also be used for manual control and centralized lubrication of lead screws, feed screws and light load guide rails.
3. Spindles, bearings and clutches: spindles, bearings and clutches, refined mineral oil, additives to improve their corrosion resistance and oxidation resistance, FC2, FC5, FC10, FC22, sliding bearings or rolling bearings and pressure, oil bath and oil mist lubrication of relevant clutches. In systems with clutches, due to the risk of corrosion, it is necessary to use products without anti-wear and extreme pressure agents; Spindle, bearing, refined mineral oil, and additives to improve their corrosion resistance, anti-oxidation and anti-wear properties, FD2, FD5, FD10, FD22, pressure, oil bath and oil mist lubrication of sliding bearings or rolling bearings, can also be used for lubrication of parts requiring low oil viscosity, such as precision machinery, hydraulic or pneumatic machinery, solenoid valves, oil air lubricators and hydrostatic bearings.
4. Guide rail: Refine mineral oil, and improve its lubricity and stick slip property. G68, G100, G150, G220 are used for the lubrication of sliding bearings and guide rails, especially for the lubrication of guide rails with low speed movement, so as to minimize the “creeping” phenomenon of guide rails. They can also be used for the lubrication of various sliding parts, such as lead screws, feed screws, cams, ratchets, and intermittent light duty worm gears.
5. Hydraulic system: hydraulic system, refined mineral oil, and improve its rust prevention, oxidation resistance and foam resistance, HL32, HL46, HL68; Refine mineral oil and improve its rust prevention, oxygen resistance, wear resistance and foam resistance. HM15, HM32, HM46, HM68, including the general hydraulic system of heavy load components, are also suitable for lubrication of sliding bearings, rolling bearings and various normal loads and gears (except worm gears and hypoid gears). HM32 and HM68 can respectively replace CKB32 and CKB68; Refine mineral oil, and improve its rust prevention, oxygen resistance, viscosity temperature resistance and foam resistance. HV22, HV32, HV46, CNC machine tools. In some cases, HV oil can replace HM oil. Hydraulic and guide rail system, refined mineral oil, and improved its rust prevention, anti-oxidation, anti-wear, anti foam and visco slip properties. HG32 and HG68 are used for machinery combined with sliding bearing and hydraulic guide rail lubrication system to reduce the “creeping” phenomenon of the guide rail at low speed. If the viscosity of the oil is appropriate, it can also be used for a separate guide rail system. HG68 can replace G68.
6. Where to use lubricating grease: general lubricating grease, and improve its oxygen resistance and corrosion resistance, XBA or XEB1, XEB2, XEB3, general rolling bearings, open gears and various parts to be greased.
Note: code description: AN – total loss system oil, CKB – anti-oxidation and antirust industrial gear oil, CKC – medium load industrial gear oil, FC – bearing oil, FD – FC bearing oil for improving antiwear property, G – guide rail oil, HL hydraulic oil, HM hydraulic oil (antiwear type), HV low-temperature hydraulic oil, HG – hydraulic guide rail oil, XBA – anti-oxidation and antirust grease, XEB – anti-oxidation, antirust and antiwear grease.