Mold costs depe…
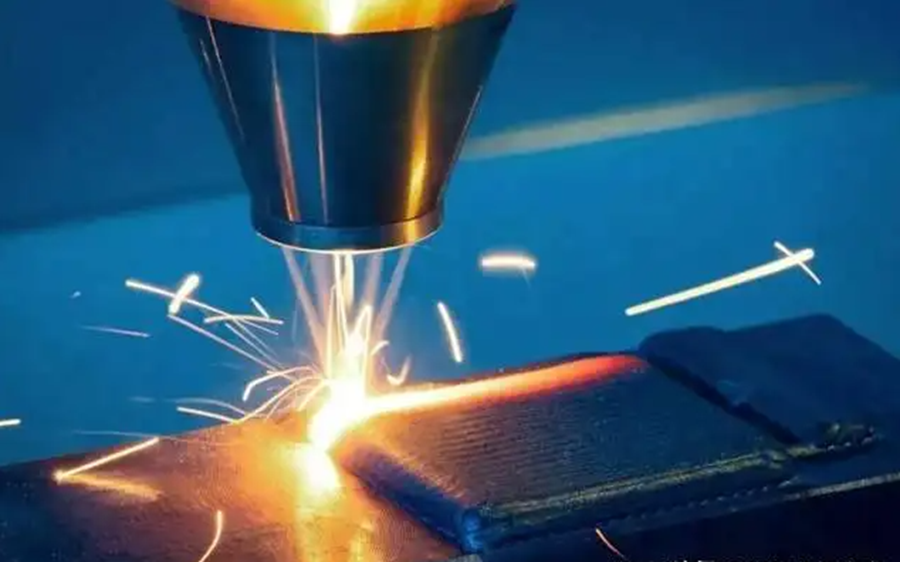
Complete Surface Treatment! Which materials are suitable for different surface treatments? Which products are commonly used?
01 Vacuum Plating
Vacuum electroplating is a physical deposition phenomenon. That is, argon is injected in a vacuum state, and the argon hits the target. The target is separated into molecules, which are absorbed by conductive goods to form a uniform and smooth metal like surface layer.
Advantages: high quality, high brightness and product surface protective layer
Typical applications: surface treatment of reflective coatings, consumer electronics and heat shields
Applicable materials:
1. Many materials can be vacuum plated, including metal, soft and hard plastics, composite materials, ceramics and glass. Among them, aluminum is the most commonly used for electroplating surface treatment, followed by silver and copper.
2. Natural materials are not suitable for vacuum electroplating, because the moisture of natural materials will affect the vacuum environment.
02 Electrolytic polishing
Electrolytic polishing takes the workpiece to be polished as the anode and insoluble metal as the cathode. The two poles are immersed into the electrolytic cell at the same time to produce selective anodic dissolution through DC ionization reaction, so as to achieve the effect of removing fine burrs on the workpiece surface and increasing the brightness.
Advantages: bright, smooth and sanitary surface
Typical applications: building structures, food handling and storage, and medical pharmacy
Applicable materials:
1. Most metals can be electropolished, and most commonly used for surface polishing of stainless steel (especially for austenitic nuclear grade stainless steel).
2. Different materials cannot be electropolished at the same time, or even put in the same electrolytic solvent.
03 Photoetching surface treatment
Photoetching surface treatment is called photoetching for short. It uses photographic means to make an anti-corrosive film image to protect the surface. It is a method of using chemical etchants to etch metal, plastic, etc. to produce surface texture.
Advantages: Photoetching surface treatment can be realized with extended exposure and chemicals
Typical application: used for surface treatment of jewelry, nameplates and trophies
Applicable materials
1. Most metals are suitable for photo etching surface treatment. The most common are stainless steel, mild steel, aluminum, brass, nickel, tin, copper and silver. Among them, aluminum has the fastest photo etching speed, while stainless steel has the slowest photo etching speed.
2. Glass and ceramics are also suitable for photo etching surface treatment, but different photo inhibitors and chemicals are required.
04 pad printing
The pad printing process can print words, graphics and images on the surface of irregular objects, and is now becoming an important special printing.
Advantages: clear printing details can be achieved, even on uneven surfaces
Typical application: used for surface printing of vehicle interior, electronic consumer products and sports equipment
Applicable materials: pad printing process can be used for almost all materials, except for materials softer than silicone pad, such as PTFE.
05 Galvanizing
Galvanizing process is a surface treatment technology to coat a layer of zinc on the surface of iron and steel alloy materials for aesthetic, rust prevention, etc. The zinc layer on the surface is an electrochemical protective layer, which can prevent metal corrosion. The main methods are hot galvanizing and electro galvanizing.
Advantages: perfect protective layer, the appearance largely depends on the quality of steel
Typical applications: surface treatment of buildings, bridges, vehicles and furniture
Applicable materials: as the galvanizing process depends on metallurgical combination technology, it is only suitable for surface treatment of steel and iron.
06 Electroplating
Electroplating is a process that uses electrolysis to attach a layer of metal film to the surface of parts, so as to prevent metal oxidation, improve wear resistance, conductivity, reflectivity, corrosion resistance and improve aesthetics. Many coins are also plated on the outer layer.
Advantages: high glossiness, corrosion resistance
Typical applications: surface treatment of vehicles, consumer electronics, furniture, jewelry and silver
Applicable materials:
1. Most metals can be plated, but different metals have different levels of purity and plating efficiency. Among them, the most common ones are: tin, chromium, nickel, silver, gold and rhodium (rhodium: a kind of platinum, extremely expensive and can maintain high brightness for a long time, which can resist most chemical substances and acids. It is most commonly used for products requiring high surface gloss, such as trophies and medals).
2. The plastic most commonly used for electroplating is ABS, because ABS can withstand the electroplating high temperature of 60 ° C (140 ° F), and its electroplated coating and non electroplated coating have high bonding strength.
3. Nickel metal should not be used for electroplating products that contact skin, because nickel is irritating and toxic to skin.
07 Powder spraying
Powder spraying is a dry spraying method. It is used on some metal workpieces by spraying or fluidized bed. The powder is adsorbed on the surface of the workpieces by static electricity. When it is completely dry, a protective film will be formed on the surface.
Advantages: the product surface is painted smoothly and evenly
Typical applications: painting of vehicles, buildings and white household appliances
Applicable materials: although it is suitable for surface spraying of some metal parts, plastics and glass, powder spraying is mainly used for protecting or coloring aluminum and steel.
08 Water transfer printing
Water transfer printing is a way to use water pressure to print the color patterns on the transfer paper on the surface of three-dimensional products. With the improvement of people’s requirements for product packaging and surface decoration, water transfer printing is used more and more widely.
Advantages: the product surface texture is precise and clear, but there will be slight stretching
Typical applications: vehicles, consumer electronics, military products, etc
Applicable materials: all hard materials are suitable for water transfer printing, and materials suitable for spraying must also be suitable for water transfer printing. The most common are injection molded parts and metal parts.
09 Screen printing
Screen printing is to transfer the ink to the substrate through the mesh of the graphic part through the extrusion of the scraper to form the same graphic as the original. The screen printing equipment is simple, easy to operate, simple and cheap in printing and plate making, and has strong adaptability. Screen printing has a wide range of applications. Common prints include: color oil paintings, posters, business cards, binding covers, commodity signs, printing and dyeing textiles, etc.
Advantages: high quality and precision of pattern details
Typical application: for clothing, electronic products and packaging
Applicable materials: almost all materials can be screen printed, including paper, plastic, metal, ceramics and glass.
10 Anodizing
Anodic oxidation is mainly the anodic oxidation of aluminum, which is to generate a layer of Al2O3 (aluminum oxide) film on the surface of aluminum and aluminum alloy by using the electrochemical principle. This oxide film has special characteristics such as protection, decoration, insulation, wear resistance, etc
Advantages: the oxide film has special characteristics such as protection, decoration, insulation, wear resistance, etc
Typical applications: mobile phones, computers and other electronic products, mechanical parts, aircraft and automobile parts, precision instruments and radio equipment, daily necessities and architectural decoration
Applicable materials: aluminum, aluminum alloy and other aluminum products.
11 Electrophoresis
Charged particles move towards their typical opposite electrodes under the action of electric field, which is called electrophoresis
Advantages: The product presents various colors, maintains metallic luster, and enhances surface performance, with good anti-corrosion performance
Typical applications: automobile, building materials, hardware, household appliances, etc
Applicable materials: stainless steel, aluminum alloy, etc.
12 Micro arc oxidation (MAO)
Micro arc oxidation (MAO), also known as micro plasma oxidation, is to grow ceramic film mainly composed of matrix metal oxides on the surface of aluminum, magnesium, titanium and their alloys by the combination of electrolyte and corresponding electrical parameters, relying on the instantaneous high temperature and high pressure effect generated by arc discharge
Advantages: high surface hardness and good wear resistance
Typical applications: aerospace field, IT products
Applicable materials: Al, Ti, Zn, Zr, Mg, Nb, and their alloys.
13 Metal wire drawing
Metal wire drawing is a surface treatment method that forms lines on the workpiece surface by grinding products to achieve decorative effect. According to the different lines after wire drawing, it can be divided into: straight wire drawing, random wire drawing, ripple, and spiral
Advantages: wire drawing treatment can make the metal surface obtain non mirror metallic luster, and at the same time, wire drawing treatment can also eliminate subtle defects on the metal surface
Typical applications: such as elevator door panels, faucets, handles, etc., kitchen appliances such as range hoods, sinks, etc
Applicable materials: almost all materials can use metal wire drawing process.
14 Decoration in mold
Decorative technology is a forming method that puts the printed film into the metal mold, injects the resin for forming into the metal mold and joins with the film, so that the printed film and the resin form a whole and solidify into a finished product
Advantages: it can be used for complex images, products are resistant to friction, prevent surface scratches, and can keep the color bright for a long time and not fade easily
Typical applications: decoration and function control panel of household appliances, automobile dashboard, air conditioning panel, mobile phone shell/lens, washing machine, refrigerator, etc
Applicable material: plastic surface.