Mold costs depe…
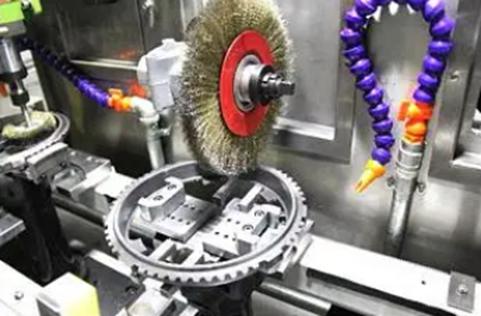
Discussion on deburring methods of machining!
1. The universality and harmfulness of burrs
Burr is an inevitable product of metal processing, which is difficult to avoid completely. The existence of burr not only affects the appearance of the product, but also affects the assembly and service performance of the product, speeds up the wear between equipment and reduces the service life. With the development of high technology and the improvement of product performance, the requirements for product quality become more and more strict, and deburring of mechanical parts becomes more and more important. The existence of burr has a great impact on product quality, product assembly, use, dimensional accuracy, shape and position accuracy, and in serious cases, the whole set of products will be scrapped, and the whole machine will be unable to operate.
2. What is burr?
Burr refers to a kind of redundant iron filings generated at the product processing edge due to extrusion deformation of metal materials during processing, commonly known as flash, which are formed during cutting, grinding, milling and other similar chip processing.
3. How to remove burrs?
So far, the method to solve the burr is to add the process of burr removal after the product processing. Now there are two main methods for deburring: chemical deburring and physical deburring. Chemistry is mainly used for precision core workpieces with complex shape, deformity, high precision requirements and high cost performance. The physical type is used for parts with rough surface, low dimensional accuracy requirements, and easy to remove by manual operation.
Chemical deburring process is a kind of immersion process, through which the effect of deburring can be achieved. This process originates from Germany and is widely used in the fields of automobile, aerospace, metal parts processing, etc. The suitable workpiece is generally automobile parts; Stamping parts; Parts of oil pump nozzle; Textile parts; Gear parts; Bearing parts; Electronic components; Bearing parts; Transmission parts; a fastening; CNC machining parts and so on. This process mainly uses the difference between the burr and the structure of the workpiece itself to achieve the effect of burr removal through the principle of vertical reaction. Our definition of burr refers to the workpiece with the thickness of burr less than 20 wires, which has nothing to do with the height of burr.
Compared with traditional deburring, this process is far superior to the traditional process in reliability, repeatability, stability, environmental protection, etc; It is efficient and time-saving, improves the surface finish of the product, safe and reliable, environmentally friendly and economical, and easy to operate, which can enhance the corrosion resistance of the product.
Physical deburring mainly includes: rough (hard contact) cutting, grinding, file, scraper, ordinary (soft contact), abrasive belt grinding, grinding, elastic grinding wheel grinding, polishing and washing, and other processes with different degrees of automation. The quality of the processed workpiece is often not guaranteed; Production costs and personnel costs are very high.
When choosing the deburring method, we should consider many factors, such as the material characteristics, structural shape, size and precision of parts, especially the influence of changes in surface roughness, size tolerance, deformation and residual stress.
4. Let’s see what netizens say about burr!
Netizen 1: The electrolyte in the electrolytic deburring has a certain corrosivity. After deburring, the workpiece should be cleaned and antirust treated. Electrolytic deburring is applicable to deburring of cross holes in concealed parts or parts with complex shapes. It has high production efficiency and short deburring time. This method is applicable to deburring of gears, splines, connecting rods, valve bodies, crankshaft oil path orifices, and sharp corners rounding. The disadvantage is that accessories with burrs are also subject to electrolysis, and the surface will lose its original luster, even affecting the dimensional accuracy.
Netizen 2: Burr, who has fought in the metal industry, must be familiar with it. It is ubiquitous in the processing of metal products. No matter how sophisticated equipment you use, it will accompany the products.
Netizen 3: Manual deburring method: 1. Prepare the parts to be deburred, alloy files and other tools. 2. Hold the file in hand, contact with the burr edge, and incline 5-10 degrees. It is easy to scratch the part surface horizontally, and chamfer the edge line if the angle is too high. 3. Use a little force to grind off the burr, and complete the deburring of the whole part in a certain order, such as the front side first and then the back side. 4. Check whether burrs are removed.
Netizen 4: The so-called burr is mainly a kind of superfluous iron filings generated at the processing edge of the processed material due to the plastic deformation of the material, especially the material with good ductility or toughness, which is particularly prone to burr, and the Chacha burr problem is one of the problems that engineers in the metal processing industry can not solve so far.
Netizen5: An electrochemical machining method that uses electrolysis to remove the burrs of metal parts, that is, place the tool cathode (usually brass) near the parts with burrs on the workpiece, with a certain gap between them (generally 0.3-1 mm). The conductive part of the cathode of the tool is aligned with the edge of the burr, and the other parts are covered with an insulating layer, so that the electrolysis effect is concentrated on the burr part. During processing, the cathode of the workpiece is connected to the negative pole of the DC power supply, and the workpiece is connected to the positive pole of the DC power supply. Low voltage electrolyte (generally sodium nitrate or sodium chlorate aqueous solution) with a pressure of 0.1-0.3 MPa flows between the workpiece and the cathode. When the DC power is turned on, the burrs will be removed by anodic dissolution and taken away by the electrolyte.
Netizen 6: Although the surface after washing and grinding looks smooth, in fact, some prominent sharp protrusions are not ground off, but are bent and laid flat on the surface of the part. There are many closed spaces under the bent tip, which inevitably contain water and air. Water and air in the confined space lead to rust, which will cause the confined space to crack again under certain conditions. This is an important inducement for corrosion and uneven peeling off of the coating or other protective layers after a period of time. The Cullygrat process acts vertically on the surface through the reaction between the liquid medicine and the parts, so it fundamentally avoids the generation of confined space. Moreover, through the improvement of the finish, the load bearing capacity of the part surface is also significantly improved.