Mold costs depe…
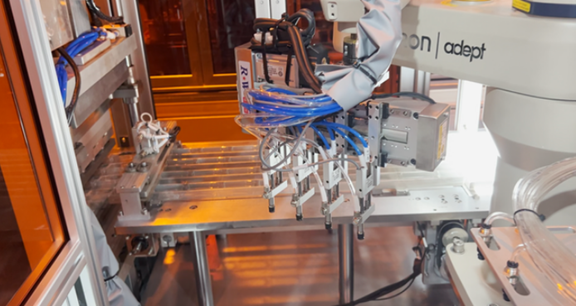
The automatic technology of Tool Repairing with CNC machining center
In machining, the cutting tool is the basic process equipment for cutting. It is in direct contact with the parts to be processed. Different cutting tools can process different part structures and parts surfaces, which plays a vital role in machining. It can be called “industrial teeth”. As a consumable, the tool itself has a certain life. Different materials and different specifications have different life; For mass production, tool consumption also occupies an important part in the processing cost. Therefore, improving tool life, controlling tool consumption, reducing processing cost and improving production efficiency are the common problems faced by manufacturing industry.
Existing technology
Tool repair is a way to improve tool life. However, the traditional manual equipment (such as manual grinder, Fig. 1) cannot meet the needs of users in terms of accuracy, efficiency, reliability and safety. At the same time, enterprises also need to train professional tool grinding personnel, which increases part of the labor cost.
technological development
In view of the above problems and in combination with the existing resources of the enterprise, a set of technical solutions for realizing tool grinding automation by using CNC machining centers are developed:
First, because the tool material is generally hard, only grinding can be used to change its shape. Grinding wheel grains of different materials are suitable for grinding tools of different materials. The size of grinding grains required for different parts of the tool is different to ensure the best combination of edge protection and machining efficiency. Therefore, the most important problem to be solved in the CNC machining center is the type and clamping mode of grinding wheel; Considering that the alumina grinding wheel is cheap and easy to be repaired into different shapes for grinding complex tools, however, the tools that can be repaired are too single (can be used for grinding HSS (high speed steel) tools), and the clamping is difficult and the replacement is frequent, so the diamond grinding wheel (can be used for grinding HSS (high speed steel), pm-hss (metallurgical powder high speed steel) and HM (hard alloy steel) tools) that can repair more tools are used. Lock the diamond grinding wheel to the tool handle of the milling cutter with the special nut, so that the diamond grinding wheel can be clamped to the cutter head of the CNC machining center and the spindle of the machine (Fig. 2).
In addition, it is necessary to consider the clamping and positioning mode of the grinding tool: the tool is clamped by the telescopic cylinder and the self-made elastic rigid jacket, and the tool clamp is fixed on the four-axis platform (as shown in Fig. 2). In this way, the parallelism and straightness of the grinding tool can be ensured by ensuring the parallelism and straightness of the four axes, and the grinding tool can be moved in the x-axis, Y-axis and a-axis directions. Coordinate with the movement of the machine spindle in the z-axis direction to realize the grinding of the cutting edge of the tool at different angles.
In addition, the most critical technology of using the CNC machining center to repair the mold tool is the use of the probe. Using the high-precision probe and the detection program input by the machining center can realize the confirmation of the tool grinding zero point, the tool grinding position and the number of grinding tool edges. The measurement results of these variables are fed back to the CNC system of the CNC machining center to input the tool grinding program prepared in advance for tool grinding (Fig. 3).
Of course, in order to realize the automation of tool grinding, we also need to add an automatic assembly line (Fig. 6): through self-design, we can get the material tray (Fig. 4) where the tools are placed, so that the robot can accurately position the tools, and then realize the loading and unloading of the tools, cooperate with the CNC processing center, the assembly line device and the final high-precision detection device (Fig. 5), and realize the complete automation of tool grinding.
The specific machining process of the grinding tool of the CNC machining center can take the grinding end milling cutter as an example: for the worn end milling cutter, the worn edge must be cut off and the required edge must be reground. Of course, it needs to ensure the effective edge length of the cutter. If it cannot be guaranteed, the end milling cutter cannot be reground. For CNC machining centers, we can set the maximum cutting length and the cutting amount each time in advance. Each time the probe is cut out for detection, the cutting amount is accumulated once; If it is detected that the blade part is still missing, it shall be cut again until the blade is complete, and other parts of the tool can be further polished; If the cutting amount exceeds the maximum cutting length, the tool cannot be reground. The next step is to grind the chip breaking groove, then grind the tool back angle, and finally grind the tool bottom edge. These can be realized in advance through the program design by using the cooperative movement between the x-axis, y-axis, Z-axis and a-axis.
summary
In short, the use of CNC machining center for tool grinding greatly improves the efficiency and accuracy of tool grinding, and also reduces the labor cost and technical requirements of tool grinding, thus further reducing the production cost of the enterprise and improving the production efficiency. It plays an indelible role in the development of tool grinding technology.