Mold costs depe…
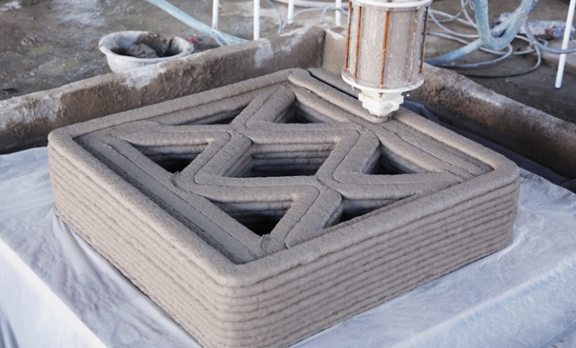
Decrypt 3D printed concrete structure and raw materials
In recent years, with the support of national policies, housing industrialization has developed rapidly. A batch of industrial houses have sprung up, and housing industrialization has entered the fast lane of development. In particular, the development of information technology has promoted the development of housing industrialization towards automation, integration and intelligence. The appearance of 3D printed concrete buildings fully shows the bright prospect of future residential industrial development. The realization of Intelligent Manufacturing in the construction industry is not a castle in the air. Not long ago, a construction company in Shanghai built two buildings with 3D printers. One is a 1100 square meter villa in Shanghai, and the other is a 6-storey residential building in Suzhou. The latter is also the highest 3D printed building in the world.
3D printing technology is an advanced manufacturing technology, which is not limited by product structure, which determines that it has sufficient application in many industries. From another perspective, 3D printing is only an advanced manufacturing technology and a tool. Its value as a product is not high, and it needs to be realized in industrial applications. It is a process in which technical advantages and user needs gradually fit. For 3D printed concrete buildings, cost, raw materials and structural safety are the key points for their future development.
3D printing concrete structure analysis
At present, the 3D printing concrete building is to carry out the modular design of the whole building, print the building industrialization module with 3D printer, and finally transport it to the construction site for assembly. Therefore, its production and construction process is basically the same as that of the PC component industrial housing. The difference is that in these 3D printed walls, slabs and other modules, there is no reinforcement. Instead, cement and glass fiber are combined to improve the tensile strength of the whole concrete structure, so as to realize the construction of 6-storey residential buildings with non reinforced concrete structures.
At present, the industrial PC structure system of domestic housing is divided into two types, one is fully assembled structure, and the other is partially cast-in-situ partially assembled structure. For example, Vanke’s R & D and assembly of integrated residential structure system is actually introduced from Japan. Its beams, columns and shear walls are cast-in-situ as load-bearing structures; The floor slab is semi prefabricated with prefabricated floor slab and cast-in-situ composite layer; Only exterior walls, stairs and balconies are fully prefabricated components. The fifth generation integrated housing of Yuanda residential engineering is similar to this. Therefore, judging from the current situation in China, most of them adopt semi prefabricated structure system, only the ambitious sustainable buildings adopt fully assembled steel structure buildings, all of which are bolted, and can be built for 6 floors in a day. A variety of new prefabricated building structure systems are also emerging.
As the most advanced and top technology in residential industrialization, 3D printing concrete buildings need to break through the semi prefabricated structure system, adopt the full assembly structure, and even 3D printing in the whole process. Only in this way can the construction industry completely transform from traditional construction to manufacturing. In addition to the basic part, 3D printing will be used in the future, including the basic part, to realize real intelligent manufacturing and use virtual assembly technology. Virtual assembly is to use computer simulation and virtual reality technology to carry out simulation assembly on the computer through the simulation model, so as to realize the optimization scheme of product process planning, manufacturing and on-site assembly.
For 3D printed building modules, the non reinforced structure is adopted to facilitate printing on the one hand, and to realize the advantages of 3D printed concrete modules in light, thin and strong on the other hand. More varieties of concrete are used to print building modules with different functions and structures. Therefore, the raw materials of 3D printed concrete have more extensive sources and more varieties. The mechanism of setting hardening and strength generation will also break through the theoretical category of traditional concrete. The durability and safety also need to be studied and demonstrated.
With the continuous development of technology, there will even be a giant 3D printer in the future, which will print the whole building on site. The main structure of the 3D printer is similar to that of the double dragon gate crane. The printer can be lifted and lowered like a tower crane. Several purlins with variable positions are arranged on the top. Each purlins is provided with a print head, and dozens to dozens of print heads are arranged according to the size of the area. The vertical structure of the building can be directly printed layer by layer. The modular structural reinforcement can be hoisted to the top by crane on the site for welding and assembly. The printing head can be used to stack concrete layer by layer with the reinforcement mesh sandwiched like the tools of ancient ramming walls. Once this giant printer appears, it will bring great changes to the whole commercial concrete industry. At the same time, it is also a huge challenge for small and medium-sized commercial concrete enterprises. This concrete technology for 3D printing is more complex and requires higher quality.
Analysis of raw materials of 3D printing concrete
According to the disclosure of public information, the 3D printed concrete buildings in Shanghai are made of glass fiber reinforced concrete, which is characterized by higher tensile, bending and crack resistance than ordinary concrete, and higher toughness and impact resistance than ordinary concrete. Therefore, it is widely used in non load-bearing components such as exterior wall panels, ceilings and partition walls, such as the white concrete grid on the exterior of the French Pavilion of Shanghai World Expo, Glass fiber concrete is used.
According to the current development trend of 3D printing concrete technology, the proportion of ordinary concrete in 3D printing building raw materials will be greatly reduced in the future. Fiber concrete, foam concrete, lightweight aggregate concrete, cement-resin-based concrete, polymer concrete, water glass concrete and other types of concrete will be applied on a larger scale, and even new material concrete may appear.
3D printing concrete is different from traditional concrete. Since 3D printing has no template, it not only needs to meet the requirements of rapid prototyping, that is, it will quickly coagulate and flow around from the printing head; It is necessary to meet the tight connection between layers of concrete without generating cold joints, and 3D printed concrete components or buildings are integrated; In addition, the concrete shall flow freely in the pipe and nozzle without blocking the pipe and nozzle. These three points require that 3D printed concrete is different from traditional concrete, and its raw materials and quality requirements are also different.
From the perspective of cementitious materials, the cementitious materials used in 3D printing concrete are very wide, which are concrete in a broad sense, not ordinary cement concrete. In addition to cement, tree finger, water glass, gypsum and Geopolymer can be used as cementitious materials for 3D printed concrete. Among them, geopolymer is more suitable for 3D printed concrete because of its characteristics of fast hardening and early strength.
Aggregate is the material with the largest proportion in concrete. 3D printed concrete has higher requirements on aggregate than traditional concrete. Aggregates with high strength, small density and particle morphology close to spherical shape are the most suitable for 3D printing concrete. Meanwhile, 3D printing concrete buildings are stacked by layers of concrete, and each layer of concrete is relatively thin. In addition, the structure of 3D printer nozzle is complex, so the aggregate particle size in concrete is required to be smaller than that of traditional concrete, and the maximum particle size of aggregate should be less than 10mm. The requirements for particle gradation, mud content, harmful substance content and other indicators are more stringent. These are determined by the particularity of 3D printed concrete.
Admixtures, which account for the smallest proportion in the composition of concrete, have significantly improved the performance of concrete. 3D printed concrete requires higher working performance, excellent fluidity in the pipe, and rapid solidification in the air after coming out of the nozzle. Therefore, it is necessary to require that the admixtures have multiple functions and must be a composite superplasticizer. In addition, the materials used for 3D printing concrete are complex and diverse, which requires its admixture to have good adaptability and form a special purpose for 3D printing.
With the development of housing industrialization and information technology, a new form of architecture has emerged, that is, 3D printing architecture. 3D printing building is a very complex system engineering, which inherits the ideas of assembly line production and intelligent manufacturing in manufacturing industry, completely breaks the restriction that industrial production cannot be adopted in building construction, and provides unlimited possibilities for the development of building industrialization. The realization of 3D printing concrete building is an inevitable trend of the development of housing industrialization, a necessary requirement to adapt to the development of modern building technology, and an important way to improve the technical level and technological innovation of the entire construction industry.
The development of 3D printing concrete technology is both an opportunity and an unprecedented challenge to the commercial concrete industry. Only by adhering to technological innovation and following the development trend of building technology, can we win the first opportunity in the future commercial concrete market competition and achieve sustainable and healthy development.