Mold costs depe…
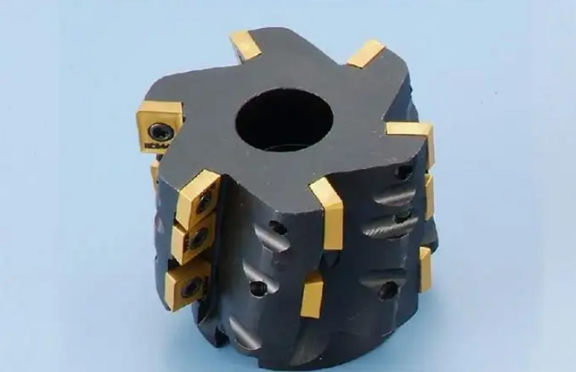
What is a cylindrical milling cutter? What is the difference with end mills?
What is a cylindrical milling cutter? A milling cutter is a rotary cutter with one or more cutter teeth for milling. We commonly use 45 degree chamfering milling cutter for machining plane on horizontal milling machine. The cylindrical milling cutter has the cutter teeth distributed on the circumference of the milling cutter. Cylindrical milling cutters are divided into straight teeth and spiral teeth according to the tooth shape, and coarse teeth and fine teeth according to the number of teeth. The spiral tooth coarse tooth milling cutter has few teeth, high tooth strength and large chip space, which is suitable for rough machining, and the fine tooth milling cutter is suitable for fine machining. Multiple milling cutters can be combined for wide plane milling, and the combination must be left and right staggered spiral teeth.
High productivity of cylindrical milling cutter the milling cutter rotates continuously during milling and allows higher milling speed, thus having higher productivity. During continuous cutting and milling, each cutter tooth is cutting continuously, especially for end milling, the milling force fluctuates greatly, so vibration is inevitable. When the frequency of vibration is the same or multiple of the natural frequency of the machine tool, the vibration is the most serious. In addition, when high-speed milling, the cutter teeth also undergo periodic cold and hot impact, which is prone to crack and edge collapse, which reduces the tool durability. The multi cutter and multi edge cutting milling cutter has many teeth and the total length of the cutting edge is large, which is conducive to improving the durability and productivity of the cutter, and has many advantages. However, there are also the following two problems: first, the cutter teeth are prone to radial runout, which will cause unequal load of the cutter teeth, uneven wear and affect the quality of the machined surface; Second, the chip space of the cutter teeth must be sufficient, otherwise the cutter teeth will be damaged. Different milling methods according to different processing conditions, different milling methods can be selected to improve tool durability and productivity, such as up milling, down milling, symmetric milling, asymmetric milling, etc.
Besides cylindrical milling cutter, end milling cutter is also commonly used. What is the difference between cylindrical milling cutter and end milling cutter? The most direct difference is that the cylindrical milling cutter should be used on the cutter bar, and the end milling cutter can be directly inserted into the taper hole of the spindle. The end milling cutter is used to process grooves and step surfaces. The cutter teeth are on the circumference and end face, and cannot be fed along the axial direction during normal operation. When there are end teeth passing through the center on the end milling cutter, it can be fed axially. Moreover, the use range and requirements of high-speed steel end mills are relatively wide, and even if the cutting conditions are slightly inappropriate, there will not be too many problems. While the carbide end milling cutter has good wear resistance in high-speed cutting, its application range is not as wide as that of high-speed steel end milling cutter, and the cutting conditions must strictly meet the use requirements of the cutter.
However, when using cylindrical milling cutter or end milling cutter, it should depend on the materials we process and the amount of processing. When we buy these products, the manufacturer will give you relevant suggestions. You can refer to them. If you want to know more about cylindrical milling cutter. Please continue to pay attention to the quick access network. The editor will recommend relevant content for you.