Mold costs depe…
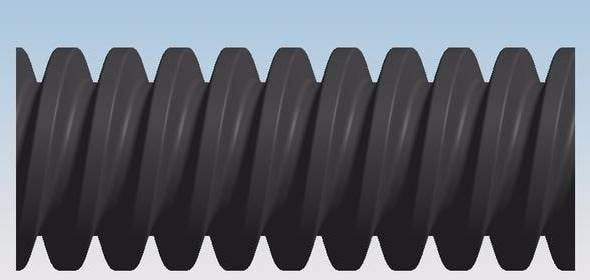
Method of NC high speed turning trapezoidal thread
There are certain technical difficulties in machining trapezoidal thread on CNC lathe, especially in high-speed cutting. It is not easy to observe and control during processing, and the safety and reliability are also poor. This requires correct tool geometry and processing technology, and introduces an efficient and feasible processing method.
Whether it is on an ordinary lathe or a numerical control lathe, it is always difficult for secondary and higher vocational students to process trapezoidal threads. In particular, the high-speed turning of trapezoidal threads on a numerical control lathe has not been introduced in most books and textbooks. It is difficult for students to master its fine calculation and reasonable processing technology. The author will focus on the high-speed turning method of trapezoidal thread according to the examination questions of Hunan Province vocational skill appraisal senior workers in recent years, combined with my own experience and experience.
1、 Selection of processing methods
As shown in Fig. 1, when machining trapezoidal threads on the CNC lathe, the three jaw chuck adopts the method of one clamp and one top. For the convenience of tool setting and programming, the program origin is set at the center point of the right end face of the workpiece. In addition, the tool setting template is also self-made to facilitate the accuracy of Z direction when changing tools in rough and fine turning. It should be pointed out that because of the high-speed machining of trapezoidal thread, the carbide tool is selected.
When turning trapezoidal thread at high speed, because the pitch is too large, it is required that the cutting force should not be too large when machining trapezoidal thread, and the tool should not cut three sides at the same time, in order to prevent “stabbing” and “breaking edge”. Through many years of practice, the author has proved that the thread cutting instructions G32 and G92 can not be used to carry out the straight forward method or the straight forward groove cutting method on the economic type CNC lathe. Even though the left-right swing method of G92 combined with subroutine introduced in many magazines in recent years is not the best method to carry out the layered cutting, this method can theoretically make the cutting force small, but it ignores that most of our commonly used lathes are economic type CNC lathes, However, the control system of the economical numerical control lathe is semi closed loop, so that the servo system can not keep up with the numerical requirements of the numerical control system when swinging left and right, thus changing the machining pitch. In consideration of programming and machining, combined with practical experience, I think it is a good, safe, reliable and easy method to use the thread cutting compound cycle instruction G76 to process.
2、 Introduction to G76 instruction
G76 command is oblique cutting. Since it is one-sided cutting, the tool load is small, chip removal is easy, and the cutting depth is decreasing. General large pitch thread processing.
1. G76 command feed path and feed assignment. (Figure 2)
Group diagram: various parameters of trapezoidal thread processing
Feed rate per time = H / √ n-1 × √¢, where h is the total height of the thread thread, n is the number of feeds, III is the first feed = ⊿ D, is the second feed = 1, and the third and more feeds = X-1
2. Format:
G76 P(m)(r)(a) Q(⊿dmin) R(d)
G76 X(U) Z(W) R(i) P(k) Q(⊿d ) F(L)
Wherein:
M – number of finishing repetitions, 1-99 times.
R – chamfering amount of thread tail (oblique tool withdrawal), 00-99 units, if 01 is taken as 0.11 × Lead.
A – angle of thread tip (thread profile angle). 80, 60, 55, 30, 29, 0 degrees can be selected.
⊿ Dmin – Minimum back cutting amount during cutting, radius value, μ M.
D-finishing allowance, radius value, mm.
I-radius difference of thread part, radius value, μ M.
K – thread depth, as per H = 0 65 × Pitch (P) calculation, microns.
⊿ D – first cutting depth, radius value, micron.
L – thread lead, micron.
3、 Selection of tool geometry
According to the condition of high-speed turning trapezoidal thread, the helix angle is calculated first, so as to correct the geometric angle of grinding tool. Helix angle is a = [P / (d)] = arctan [5 / (3.14) × 25.5)] = 3.82, so it is appropriate to select the left rear angle of 6-8 degrees and the right rear angle of 2 degrees; In order to facilitate chip removal and prevent the tool from being damaged, the rake angle is taken as 6-8 degrees to make the tool sharper and conducive to chip breaking. It is particularly pointed out that I use rough turning and fine turning tools. Since rough machining is easy to damage and wear the turning tool, I grind the sharp corner edge of the rough turning tool into an arc shape, which can strengthen the strength of the tool tip. Even if the rough machining amount is too large, there is a certain safety factor, while the fine machining is completely grinded according to the thread shape. Attention should be paid to the accuracy of the zero point when the coarse and fine turning tool is aligned in the Z direction. The geometric shapes of rough and fine turning tools are as follows:
4、 Preparation of procedures.
This paper only describes the programming of trapezoidal thread, as follows:
%0003;
N10 G90 G95;
N20 M3 S350 T0505;
N30 G0 X35. Z-10.;
N40 G76 P020030 Q20 R0.02
G76 X22.3 Z-94. P2750 Q329 F5.
N50 G0 X120. Z200.;
N60 M5;
N70 M30;
5、 Matters needing attention in machining with thread compound cutting cycle G76.
When machining trapezoidal thread by numerical control lathe, due to the change of its transmission chain, in principle, the rotation speed can only ensure that the tool will be displaced by one lead along the direction of the main feed shaft when the spindle rotates for one cycle. It should not be restricted, but it will be affected by the following aspects:
1. The thread pitch / lead value commanded in the thread processing program section is equivalent to the feed rate expressed by the feed rate per revolution. If the spindle speed of the machine tool is selected too high, the feed rate after conversion must greatly exceed the maximum feed rate allowed by the machine tool parameters. At this time, the machine tool will process according to the “limit thread pitch” (limit thread pitch = maximum feed rate / speed).
2. The tool is always constrained by the rising / falling frequency of the servo drive system and the interpolation speed of the numerical control device. Because the up / down frequency characteristics can not meet the processing requirements, the pitch of some screw teeth may not meet the requirements due to the “lead” and “lag” caused by the main feed motion; Turning thread must be realized by the synchronous operation function of the spindle, that is, turning thread requires a spindle pulse generator encoder. When the spindle speed is too high, the positioning pulse sent by the encoder (i.e. a reference pulse signal sent by the spindle every revolution) may be “overshoot”, especially when the quality of the encoder is unstable, it will lead to disordered threading of the workpiece.
Therefore, when turning trapezoidal thread, the spindle speed shall be selected according to the following principles:
1. Under the condition of ensuring production efficiency and normal cutting, the highest machining speed should be obtained according to the calculation formula of “limit pitch”, and the lower spindle speed should be selected;
2. When the lead-in length and cut-out length in the thread processing program section are small, the relatively low spindle speed is selected;
3. When the allowable working speed specified by the encoder exceeds the maximum speed of the spindle specified by the machine tool, a higher spindle speed can be selected as far as possible;
4. In general, the spindle speed during threading shall be determined according to the calculation formula specified in the machine tool or CNC system specification.
It should also be noted that:
1. The constant surface cutting speed control command G96 should not be used during thread cutting because the spindle speed may change and the correct pitch may not be cut.
2. During thread cutting, the feed rate is invalid (fixed at 100%) and the speed is fixed at 100%.
3. Chamfer or rounding cannot be specified in the previous segment of the thread cutting segment.
4. Usually, due to the lag of the servo system and other reasons, incorrect lead will be generated at the start and end of thread cutting. Therefore, the start and end positions of the thread should be longer than the specified thread length.