Mold costs depe…
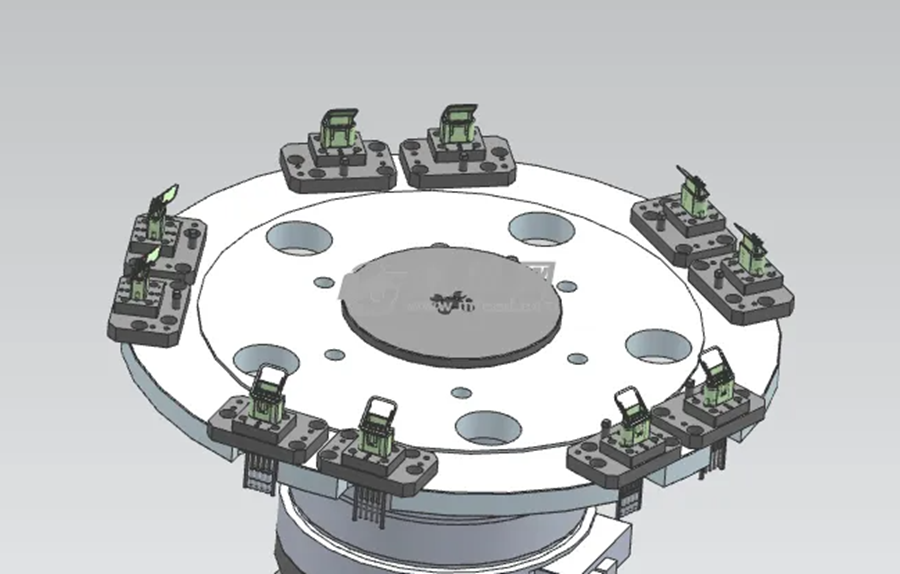
10 assembly rules to follow
1. Minimize the number of parts
Find ways to assemble parts. For example, many electronics enclosures use movable hinges instead of knuckle hinges. When routing, select a molded guide feature or use a thermoformed guide (such as an old LazerTag gun). Speaking of minimizing the number of parts
2. Built in fasteners
Whenever possible, build assembly features directly into the part instead of using screws. Snap fit is usually equally safe and can be assembled without tools. Sometimes screws are necessary, but the economical use of fasteners may consume up to 50% of the assembly labor. It should be noted that the snap fit may increase the cost of the injection mold, so it is important to design the part as injection friendly.
3. Use rubber roll parts
It’s great to be a product designer now. Many of our design problems have been solved! Previously, each thread had to be carefully designed, but now hundreds of standard diameters and pitches can be selected.
This goes far beyond the basic nuts and bolts. Cots cover most of the functions of spring, pin, motor, microcontroller, sensor and gear design. This not only allows you to focus on unique challenges, but also means that the manufacturing team has the tools and skills to assemble your design.
4. Use the same parts throughout the design and product family
Warning on rubber roller parts: it is not enough to use standard screws only. I have designed a robot component, one part of which has M5 x 10 mm socket head cap screws, the other part is M4. Design a 5 x 12 mm hex head screw on the other part.
I have to switch between assembly tools frequently; It is easy to confuse which screw will go where, which is a very bad idea. Don’t follow my example: Standardize parts not only on each component, but also on the entire product line. Where possible, a single tool should be used for the entire assembly.
5. Use modular design
An important application of cots and ordinary parts is modularization, which decomposes the design into smaller sub assemblies and can be used for a variety of products. Think about your first computer: you can put some pre assembled parts together – the motherboard, the hard disk, the video card, it’s easy. Another advantage is that modular design is not only good on the assembly line; They also help you extend the use time of the product on site by facilitating maintenance and upgrading.
6. Create unique connections
Speaking of desktop computer assembly, from the 1990s to the beginning of the 21st century, another great example of assembly design can be found inside and outside the computer case. Each connection is mechanically unique. The mouse cable cannot be plugged into the monitor port. The power cord port must not be confused with the keyboard cable.
Of course, what I want to show is computers of my age. On these computers, everything can be run using USB-C, which is more friendly to DFA (see Rule 4).
7. Clear direction for parts
Related to the concept of unique connection is the unique direction: if the parts to be assembled have the correct and wrong directions, please clarify which way is correct. Better yet, make it impossible for the parts to be assembled in the wrong way. For round parts, this may mean only one notch, but for more complex shapes, it can provide some opportunities for creative design. Just don’t be too creative
8. Make the parts easy to operate
Because now assembly is more and more handled by robots. The cost of automation has dropped rapidly, and robots have appeared in more assembly lines. Design your parts for easy grasping by robotic tongs and avoid using very small or flexible parts as much as possible. People on the assembly line will also appreciate this, and no one likes to insert screws with a microscope.
9. Avoid precision parts and non-contact areas
Similarly, it helps robots and people on the assembly line by making parts durable in the assembly process. If the parts are too delicate, or if they are easily damaged by natural skin oil, it is easy to cause rework. Imagine if Bruce Banner gets angry, can he still complete this assembly step in 10 seconds? If the answer is no, redesign.
10. Real world tolerance design
Finally, ensure that custom parts can be easily manufactured. Tolerance accumulates, and small changes in each operation can cause a big problem, especially when your design cannot adapt to changes.
Whenever possible, provide your process with as much error space as possible. Yes, machinists can make your parts fit within one ten thousandth, but if necessary, you will introduce very expensive machining unnecessarily. With 3D printing parts, the same considerations apply: even if the laser sintering changes, it is worth considering how to fit these tolerances together.